Securing future quality: our path to carbon-neutral steelmaking
Metallurgy and quality face new challenges: A large number of tests is necessary in advance before we can put our first electric arc furnace into operation at our Linz site in 2027 and to be able to assure our product mix. The increased use of scrap will lead to an increase in the number of alloying elements in the steel. Find out how our product mix is tested and secured by small-scale and large-scale testing.
Production diversity and initial findings
In our steelmaking plant, we currently produce roughly 240 different steel grades exclusively for strip production. A preliminary study has focused on how many of these can be produced in the electric arc furnace (EAF). The future EAF input materials (scrap 50%, HBI 25%, pig iron 25%) will result in a higher level of alloying elements (Cu, Cr, Ni, Mo, Sn) in the steel. These elements can influence mechanical and technological properties such as yield strength, tensile strength, toughness etc.
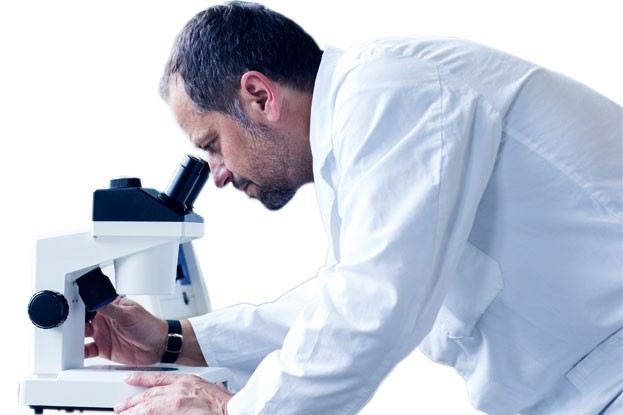
Project objectives: Reliability and assessment
- Assurance of the quality runup for startup using available raw materials and RH capacities
- Assessment of planned steel grades under the new manufacturing conditions
Procedure From lab to reality
The effects of the new production route will be assessed using a variety of different methods that will focus on comparing the new route with the conventional production route in the LD steelmaking plant. The starting point is the production of the test materials with a composition that is to be expected in the new production facility. These test materials are subjected to a variety of tests to characterize compliance with product-specific warranty values and properties during production and processing.
The material developers and quality specialists use a wide variety of testing methods in the laboratories of TSP, including tensile testing, notch impact testing, formability testing such as bending and deep drawing, delamination tests, welding suitability tests etc.
However, what sounds simple often takes quite a bit of time to implement. Different approaches are chosen for different questions.
Laboratory tests and fundamental research
Questions about the basic effects of increased alloying element content are addressed by CTE. Test materials are produced exclusively in the lab. Trial blocks weighing 12 to 90 kg are cast in our labs and those at voestalpine Stahl Donawitz. Hot rolling, cold rolling and heat treatment are performed in the lab, and the small samples are then characterized. The advantage of this small-scale manufacturing route is that many variations in composition can be carried out at a manageable cost and without disrupting regular production operations.
Large-scale testing and production conditions
Since large-scale production is different from laboratory production, production testing is also conducted during production operations. Several of the most important steel grade families (mild steels, IF steels, structural steels, microalloyed steels, multi-phase steels, tempered steels etc.) were selected. the heats in large-scale testing weigh roughly 180 tons and feature a typical alloying element for content of EAF batches that are tested by CTE.
Serial production and large-scale testing
Following joint assessment by CTE and CTQ on the feasibility of a specific steel grade from this single large-scale heat, CTQ also conducted large-scale testing on 10 other heats with the expected EAF composition. This represents a trial run that is very similar to serial production. The findings from the individual heat tests have been statistically confirmed.
Initial results and optimism
Roughly 190 heats amounting to a total weight of 34,000 tons of strip and heavy plate have been produced. No abnormalities were found with respect to slab quality and strip surfaces when compared to serial production. The strength values show a slight increase as a result of alloying elements, but this can be counteracted by slightly adjusting the steel chemistry. The team of experts in the field of metallurgy and quality see a positive future.
In a nutshell, we are working together to achieve sustainable steel production
greentec steel shows how the quality and sustainability of steel production can be ensured through systematic testing and close cooperation. Together we are creating the basis for carbon-neutral steel production and are ensuring future quality.
About greentec steel
The greentec steel project of voestalpine is an ambitious step-by-step plan that makes a valuable contribution to the achievement of the climate goals. As a first step, the voestalpine Group plans to replace two blast furnaces with two electric arc furnaces (EAFs) by the year 2027. The investment volume amounts to roughly 1.5 billion euros.
Carbon emissions can be reduced by up to 30% as early as 2029 by making this switch from the blast furnace to the EAF. This corresponds to a savings of nearly 4 million tons of CO2 per year, amounting to nearly 5% of the carbon emissions in Austria. This makes greentec steel the largest climate protection program in Austria.
The two electric-arc furnaces will enable voestalpine to produce roughly 2.5 million tons of carbon-reduced steel by the year 2027, roughly 1.6 million tons in Linz and 850,000 tons in Donawitz. Learn more about greentec steel here.