Qualität der Zukunft sichern – Der Weg zur CO2-neutralen Stahlerzeugung
Metallurgie und Qualität stellt sich neuen Herausforderungen, denn: Um unseren ersten Elektrolichtbogenofen 2027 am Standort Linz betreiben und unseren Produktmix begleiten zu können, sind im Vorfeld viele Versuche notwendig. Durch den erhöhten Einsatz von Schrott wird es zu einem Anstieg der Begleitelemente im Stahl kommen. Erfahren Sie, wie durch klein- und großtechnische Versuche unser Produktmix getestet und abgesichert wird.
Produktionsvielfalt und erste Erkenntnisse
Aktuell produzieren wir im Stahlwerk allein für die Bandfertigung regelmäßig ca. 240 verschiedene Werksmarken. In einer Vorstudie wurde untersucht, welche davon über den Elektrolichtbogenofen (EAF) darstellbar sind. Durch die künftigen EAF-Einsatzstoffe (Schrott 50%, HBI 25%, Roheisen 25%) wird es zu einem höheren Begleitelementpegel (Cu, Cr, Ni, Mo, Sn) im Stahl kommen. Diese Elemente können die mechanisch-technologischen Eigenschaften (Streckgrenze, Zugfestigkeit, Zähigkeit, etc.) beeinflussen.
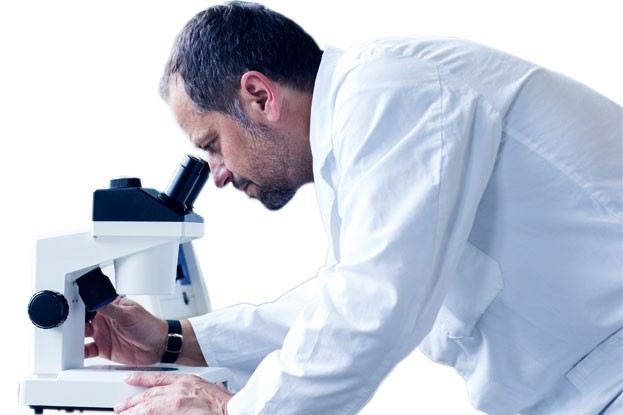
Projektziele: Absicherung und Untersuchung
- Absicherung des qualitativen Hochlaufs für das Startszenario unter Einhaltung der verfügbaren Rohstoffe und der RH-Kapazitäten
- Untersuchung der geplanten Stahlsorten unter den neuen Herstellungsbedingungen
Vorgehensweise: Vom Labor zur Realität
Die Effekte, die sich durch die geplante neue Herstellroute ergeben, werden mit vielfältigen Methoden untersucht. Der Fokus liegt dabei auf dem Vergleich zur konventionellen Herstellroute im LD-Stahlwerk. Ausgangspunkt ist jeweils die Herstellung des Versuchsmaterials mit einer Zusammensetzung, wie sie für die neue Anlage zu erwarten ist. Dieses Versuchsmaterial wird verschiedensten Tests unterworfen, um die Einhaltung der produktspezifischen Gewährleistungswerte und der Eigenschaften bei der Herstellung und Verarbeitung des Materials zu charakterisieren.
Dabei greifen die beteiligten Werkstoffentwickler und Qualitätsingenieure auf eine Vielzahl von Versuchsmethoden in den Labors von TSP zurück (Zugversuche, Kerbschlagbiegeversuche, Umformbarkeitstests wie Biegen und Tiefziehen, Untersuchung der Delaminationsneigung, Schweißeignungstests usw.).
Was sich einfach anhört, ist aber oft in der Umsetzung aufwändig. Daher werden für unterschiedliche Fragestellungen unterschiedliche Ansätze gewählt.
Laborversuche: Grundlagenforschung
Fragen zu grundlegenden Effekten erhöhter Elementgehalte werden im CTE bearbeitet. Dabei erfolgt die Versuchsmaterialproduktion zur Gänze im Labor. Versuchsblöcke von 12-90 kg werden in unseren Labors und auch bei voestalpine Stahl Donawitz abgegossen. Die nachfolgenden Prozessschritte (Warmwalzen, Kaltwalzen, Wärmebehandlung) werden in Laboranlagen durchgeführt, und die erzeugten Kleinproben werden im Anschluss charakterisiert. Der Vorteil dieser kleintechnischen Herstellroute ist, dass viele Variationen der Zusammensetzung bei überschaubaren Kosten durchgeführt werden können, ohne die laufende Produktion zu stören.
Großtechnische Versuche: Reale Produktionsbedingungen
Da reale Produktion an realen Anlagen etwas anderes ist als reine Laborproduktion, werden Versuchsproduktionen auch im Betrieb durchgeführt. Dazu wurden mehrere Vertreter der wichtigsten Stahlsortenfamilien (Weichstähle, IF-Stähle, Baustähle, mikrolegierte Stähle, Mehrphasenstähle, Vergütungsstähle, etc.) ausgewählt. In großtechnischen Versuchsprogrammen wird jeweils eine Schmelze von ca. 180 Tonnen mit typischem Begleitelementgehalt von EAF-Chargen produziert und nach Fertigproduktion von CTE untersucht.
Reif für die Serie: Absicherung durch Großversuche
Nach einer gemeinsamen Bewertung von CTE und CTQ zur Machbarkeit einer Stahlsorte aufgrund dieser großtechnischen Einzelschmelze werden von CTQ auch Großversuche im Umfang von ca. 10 Schmelzen mit der erwarteten EAF-Zusammensetzung durchgeführt. Dies stellt den Testlauf ähnlich zur Serienproduktion dar. Dabei werden die Erkenntnisse aus den Einzelschmelzenversuchen statistisch abgesichert.
Erste Ergebnisse und Optimismus
Bisher wurden ca. 190 Schmelzen mit einem Gesamtgewicht von 34.000 Tonnen Band und Grobbleche produziert. Im Vergleich zur Serienproduktion zeigten sich dabei keinerlei Auffälligkeiten hinsichtlich Brammenqualität und Bandoberflächen. Bei den Festigkeitswerten lässt sich ein leichter Anstieg aufgrund der Begleitelemente erkennen. Diesem kann aber durch eine leichte Anpassung der Stahlchemie entgegengewirkt werden. Damit blickt das Team von Metallurgie und Qualität positiv in die Zukunft.
Fazit: Gemeinsam zur nachhaltigen Stahlproduktion
greentec steel zeigt, wie durch systematische Tests und enge Zusammenarbeit die Qualität und Nachhaltigkeit der Stahlproduktion sichergestellt werden kann. Gemeinsam schaffen wir die Grundlage für eine CO2-neutrale Stahlerzeugung und sichern die Qualität der Zukunft.
Zu greentec steel
Die voestalpine hat mit greentec steel einen ambitionierten und umsetzbaren Stufenplan, um ihren Beitrag zur Erreichung der Klimaziele leisten zu können. Im ersten Schritt plant der Konzern ab 2027 zwei Hochöfen durch zwei Elektrolichtbogenöfen (EAFs) zu ersetzen. Das Investitionsvolumen dafür beträgt rund 1,5 Milliarden Euro.
Mit dem teilweisen Umstieg von der Hochofen- auf die Elektrostahlroute können bereits bis 2029 die CO2-Emissionen um rund 30 % reduziert werden. Das entspricht einer Einsparung von knapp 4 Mio. t CO2 pro Jahr – das sind fast 5 % der CO2-Emissionen Österreichs. greentec steel ist damit das größte Klimaschutzprogramm in Österreich.
Mit den beiden Elektrolichtbogenöfen kann die voestalpine ab 2027 jährlich ca. 2,5 Mio. Tonnen CO2-reduzierten Stahl produzieren, davon 1,6 Mio. Tonnen in Linz und 850.000 Tonnen in Donawitz. Mehr über greentec steel erfahren Sie hier.