Our mission: 0% CO2 emissions by 2035
Climate change is the biggest challenge of our time. We are working to meet this challenge, setting ourselves the goal to become CO2-neutral in the Metal Forming Division by 2035. Only when everyone in the value chain does their part can we jointly achieve our common goal.
Already today, numerous projects to save energy, optimize processes, source green electricity, or even to generate our own renewable energy are underway at our locations around the world, together with efforts to motivate our suppliers to implement their own climate protection measures.
Our vision: The Green Factory
In the future, it will not only be decisive what you produce as a company, but also how CO₂-intensively you produce it. That is why the Metal Forming Division has set itself the goal of achieving a CO₂-neutral production by 2035. A holistic approach and the interaction of all measures across all key areas will lead to the best sustainable result and make the Green Factory a reality. The Green Factory is the vision for each of our four business units. As the units differ in their product portfolio as well as in their processes, work steps, and manufacturing methods, the Green Factory has different detailed characteristics for each unit. Click through the business units of the Metal Forming Division and find out where and how CO₂ emissions are avoided:

Green Pre-material—greentec steel
Wind Energy
Recycling Material
Hydro Power
Green Logistics
Process Optimization:
e. g. LED Lighting
Job Bicycle
Photovoltaic Energy
E-vehicle Fleet
Cold Forming
Hot Forming
Laser Welding
Stamping
Painting
Assembly
e. g. LED Lighting

Green Pre-material—greentec steel
Wind Energy
Recycling Material
Hydro Power
Green Logistics
Job Bicycle
Photovoltaic Energy
E-vehicle Fleet
Finishing
Joining technology
Heat Treatment
Forming
Cold Rolling
Biomass energy

Green Pre-material—greentec steel
Photovoltaic Energy
Wind Energy
Recycling Material
Hydro Power
Green Logistics
Process Optimization: e. g. LED Lighting
Job Bicycle
E-vehicle Fleet
Roll Forming
Cold Drawing
Pre-processing
Painting
Slit Strip

Process Optimization: e. g. LED Lighting
Green Pre-material—greentec steel
Photovoltaic Energy
Wind Energy
Recycling Material
Hydro Power
Green Logistics
Job Bicycle
E-vehicle Fleet
Edging, Punching,
Drilling
Roll Forming
Edging, Punching,
Bohren
Engineering & Project Handling
Pre-processing
Slit Strip
Environmentally certified suppliers
Welding
Welding
Galvanizing
Assembly
Stamping
Stamping
Road Safety Systems
Half-finished Material
from Tubes & Sections
Rack Systems
Process improvements and technology changes are the royal class of CO₂ reduction. In most cases, not only CO₂ but also a lot of energy is saved here. Examples are LED lighting instead of conventional lighting, synchro motors instead of hydraulics, solid-state lasers instead of CO₂ lasers, and many more.
Large PV systems can be found on many of the Metal Forming Division's roofs. The electricity generated at the top of the roof is used to form our metals a few meters below. We want to generate up to 20% of our electricity consumption ourselves in the future. We are already well on the way to achieving this goal.
Compared to PV systems, electricity from wind turbines can be produced more efficiently and, above all, independent of the time of the day and the season. Individual plants of the Metal Forming Division have therefore concluded a long-term supply contract with a wind farm near voestalpine sites in 2023.
Hydropower is characterized by high continuity (day-night, winter-summer). One of the largest companies in the Metal Forming Division has been operating its own hydropower plants for years, which are directly connected to the plant.
The bicycle is the environmentally friendly, sporty alternative to the fossil-fueled car and is also used to cover larger distances within the company at larger production sites. In addition to bike racks, we have attractive leasing bike offers for our employees. Those, who also use their bike in their free time, are even doing something good for their health.
We have been using electric forklifts in our intralogistics for many years. With charging stations on the factory premises, both employees and business partners can charge their e-vehicles. The share of e-vehicles in the company fleet is being successively increased.
The CO2UNTDOWN TO ZERO has started!
We are producing our own electricity (in MWh/a):
Installed PV-capacity at our sites
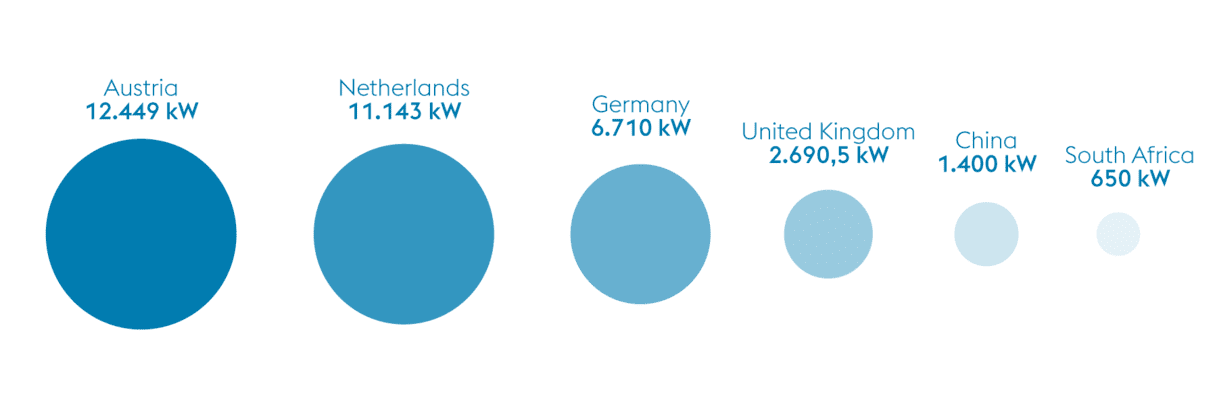
Our CO2 Roadmap
Save energy and optimize processes
Energy which is not consumed cannot create emissions—so our goal is to save energy wherever we can. We plan to achieve this by continuously improving our manufacturing processes and site infrastructures.
One method is to use the waste heat from manufacturing to heat office space, for example, or to improve building insulation.

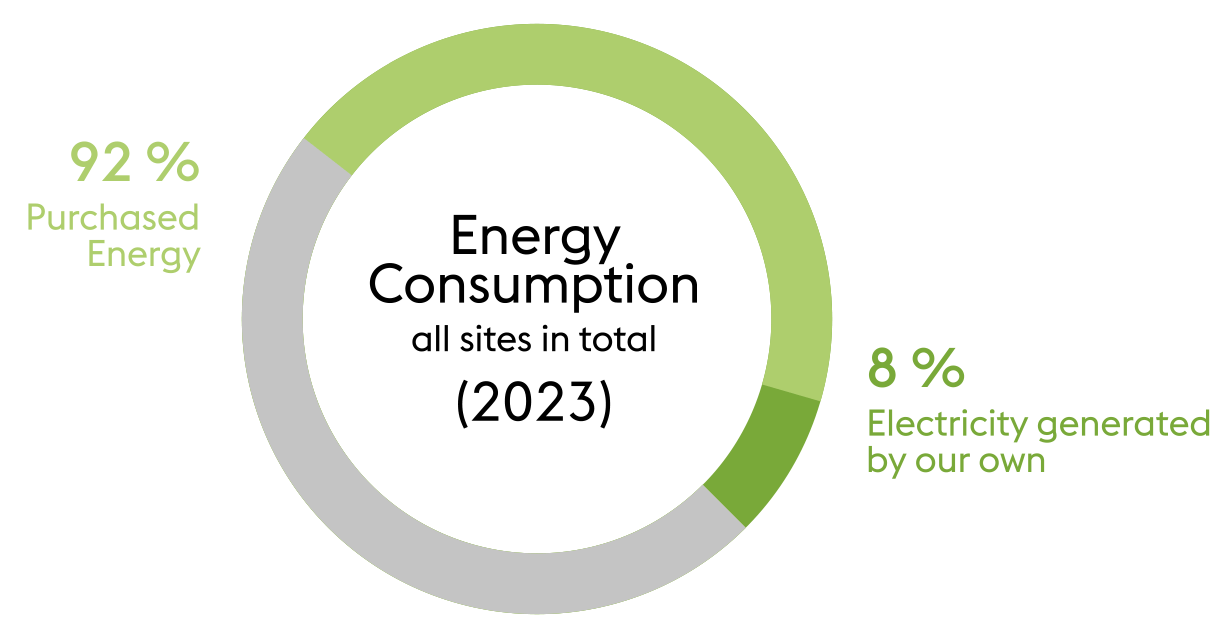
Switching to renewable energy sources
Electricity generation creates CO2 emissions—because electricity does not just simply come out of the power outlet.
That is why we have started converting to electricity generated from renewables. Locations in both Austria and Brazil are already exclusively using green electricity, and our other locations are well on their way to joining them.
Producing our own green energy
Sourcing only renewable energy is not enough for us. We also produce it directly where it is needed: at our production sites. To this end, large-scale photovoltaic systems are are installed on roofs, walls and open spaces. Where possible, we also use hydropower.
At our site in Bunschoten, the Netherlands, for example, we have installed the country’s largest photovoltaic system. Its 35,000 solar panels have saved us 5,700 tons of CO2 emissions to date.


Minimizing the CO2 footprint of our products
Emissions are not only generated during production. The production of pre-materials such as steel plate and aluminium can emit huge volumes of CO2. Freight transport also has an impact on climate.
That is why we pay careful attention to where each share of our CO2 emissions originates. We also consider how we can further reduce CO2 emissions along the entire value chain—for example, during transport, with our primary products, and by procuring materials from suppliers who, like us, have a CO2 reduction plan.
Raise environmental awareness
We want to fully exploit every opportunity to reduce CO2 and so we have established a range of projects which will serve to support this mission beyond our own operations.
CO2 is the "new currency". We still sometimes find it a little difficult to deal with this currency. Everyone knows roughly what a liter of milk, a kilo of beef, a liter of diesel or a bicycle costs. But who knows how much CO2 these products actually cause in their production? However, this knowledge of the CO2 footprint is a basis for climate-conscious action. We want to actively make a contribution and develop environmental product declarations including the CO2 footprint of our products, and even create simple CO2 calculators to help developers, employees and customers. Because those who know nothing, must believe everything. Or put differently: Who is not aware of the CO2 footprint, believes to act environmentally conscious. Test yourself: What causes more CO2? 1 kg of beef, 1 kg of steel, 1 kg of aluminum or 1 liter of milk? Are you sure?
