
alzen® - the alloy without lead
For the reduction of your CO2-footprint
alzen® 305 is a zinc-based alloy (ZnAlCu) developed by voestalpine with-out the addition of lead, which is primarily suitable for use as a bearing material and also offers other possibilities and advantages.
Compared to lead-containing red castings, this sustainable lead substitute is characterised by comparable mechanical and tribological properties, significantly lower density and a good price-performance ratio.
Advantages
- High load capacity of the ZnAlCu alloy
- Excellent emergency running property & wear-resistant
- Good embedding capacity of impurities & dirt
- No lead as an alloying element and therefore no information obligation according to REACH Regulation, Article 33
- Low density
- Excellent sliding properties with low coefficients of friction
- Very good wettability & lubricant distribution
- Higher thermal conductivity than standard leaded red bronze alloys e.g. CuSn12-C13/Gbz12, CuSn7Zn4Pb7/RG7, CuSn12-C13 / (Gbz12)14, CuSn7Zn4Pb7-C15 / (SAE66016, RG717), CuSn7Pb15-C18 / (SAE6719), CuSn10Pb10-C20 / (SAE6421), CuSn14-C22 / (B14)23 etc.
- Good damping capacity
- High processing speeds possible (similar to aluminium alloys such as EN AW-5083)
- Low sensitivity to edge pressure (comparable to Gbz12)
- Lower CO2-footprint compared to conventional gunmetal alloys


Industries & applications
Our innovative special alloy alzen® 305 is favoured by recognised companies from demanding sectors of the metal and electronics industry.
Mechanical and plant engineering | Metal industry | Rail vehicle manufacturing
- Machine tools
- Conveying systems
- Drive technology
- Agricultural machinery
- Mining, construction machinery
- Pumps and compressors
- Cooling and air technology
- Fittings
- Food processing machinery
- Textile machinery
- Ovens
- Machines for the paper industry
- Metal production and rolling mill equipment
The lead-free zinc alloy is used for various tribological applications. The spectrum ranges from sliding elements such as plates, guideways, thrust washers, bushings and bearing segments to hydraulic components such as sealing rings and other customised special parts.
Lubrication types of plain bearing

Delivery programme
alzen® 305 | Casting material
Mould casting small
- Diameter: 35 - 116 mm
- Lengths: 280 - 500 mm
- Diameter: 60 - 570 mm
- Lengths: up to 580 mm
- Block dimensions: on request
Sand casting / composite material
- Size range: on request
Delivery times
- Semi-finished products: approx. 8 weeks
- Finished parts: approx. 12 weeks
alzen® 305 | Wrought alloy
Raw sheets
Max. dimensions s x L x B [mm] | ||
s | L | B |
12 | 1300 | 1650 |
15 | 1300 | 1650 |
20 | 1300 | 1650 |
25 | 1300 | 1650 |
30 | 1300 | 1650 |
35 | 1800 | 1650 |
40 | 1800 | 1650 |
45 | 1800 | 1650 |
Rolled-in bearing segments
- Max. thickness finished parts: 31 mm
- Max. thickness raw parts: 45 mm
- Size range: on request
Sand casting / composite material
- Size range: on request
Delivery times
- Semi-finished products: approx. 8 weeks
- Finished parts: approx. 12 weeks
Packaging and surface protection
If no special agreements have been made by the time of acceptance of the order, the choice of packaging and/or surface protection for transport and storage is the responsibility of voestalpine Camtec GmbH.
Standard packaging
- Castings < 20 kg: cardboard
- Castings ≥ 20 kg: wooden boxes
- Metal sheets: disposable pallets incl. edge protection
To prevent oxidation of finished components, it is recommended that alzen® 305 finished parts are stored in a dry environment. Additional protection is provided by corrosion inhibitors such as ENSIS® RPO 600.
Plain bearings for linear, radial, thrust, spherical and combination applications
Linear bearing
Wear plates
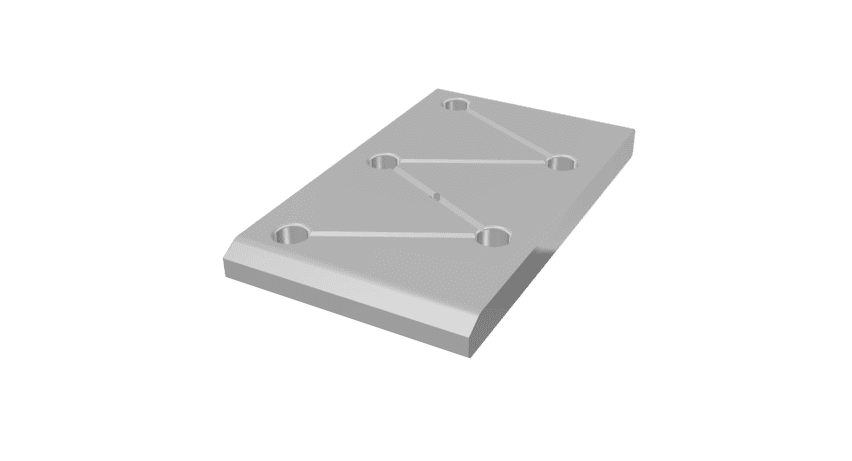
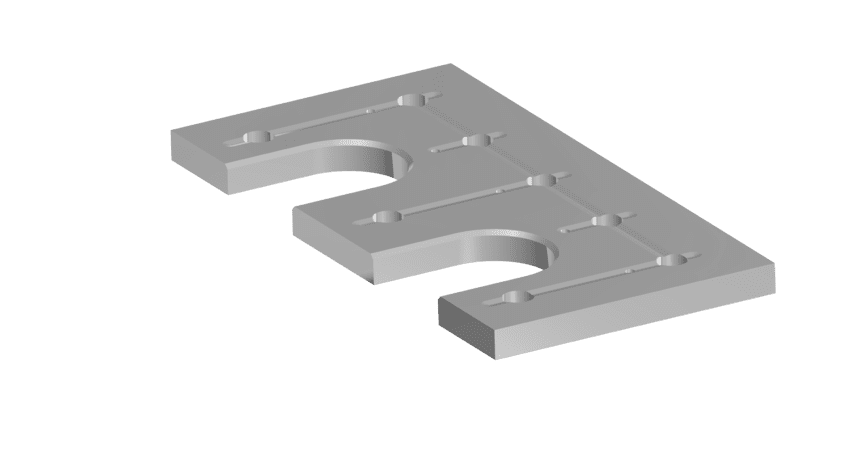
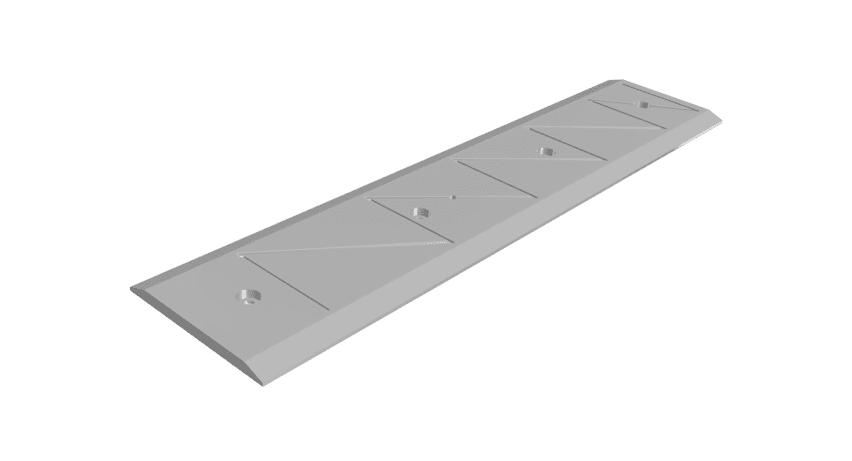
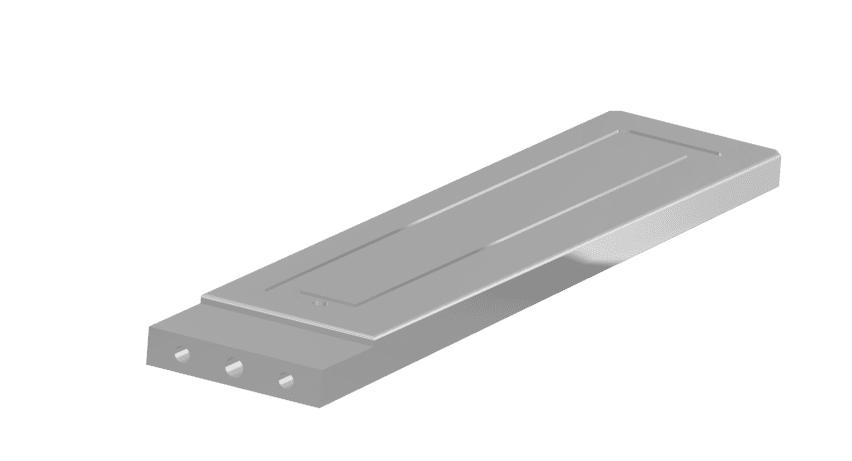
Wear strips
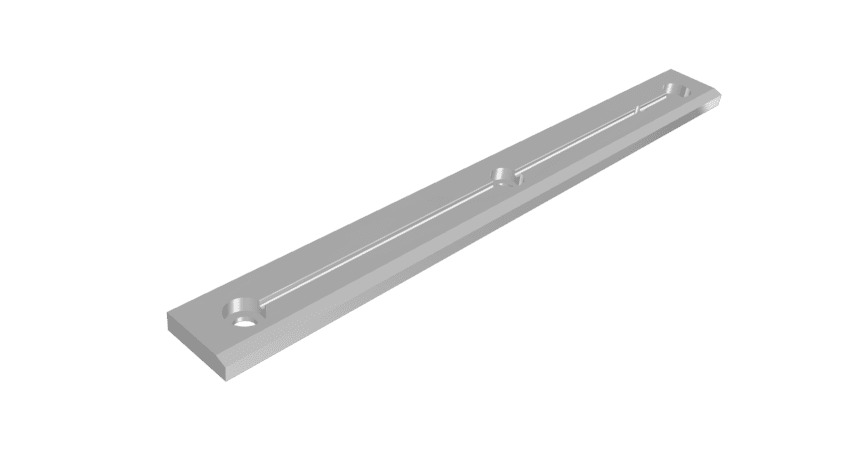
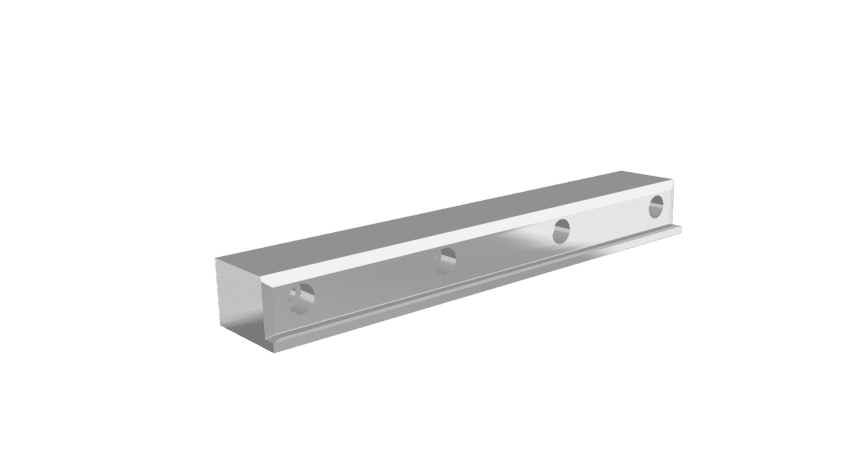
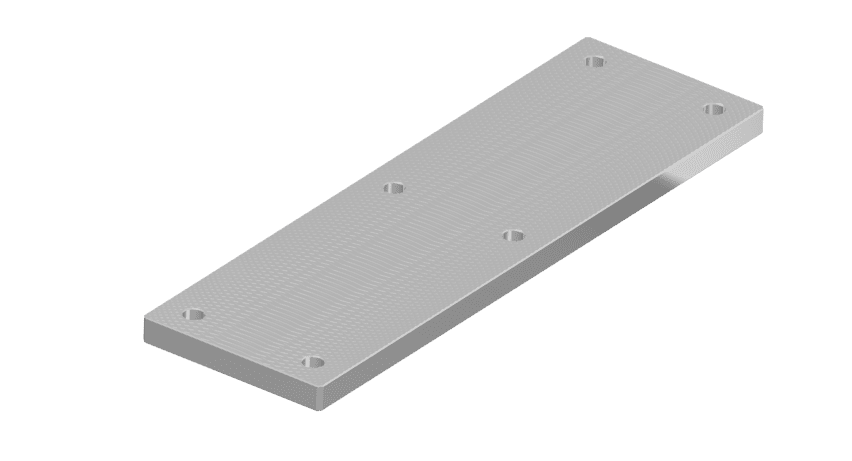
Radial bearing
Bushings without / with flange
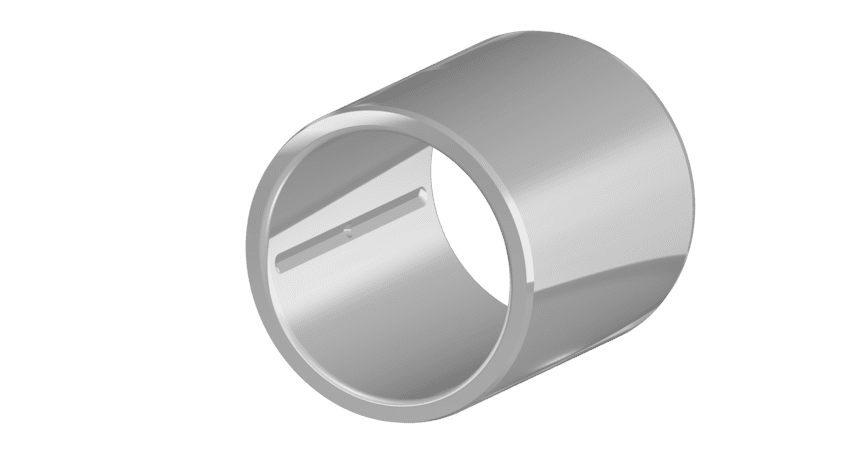
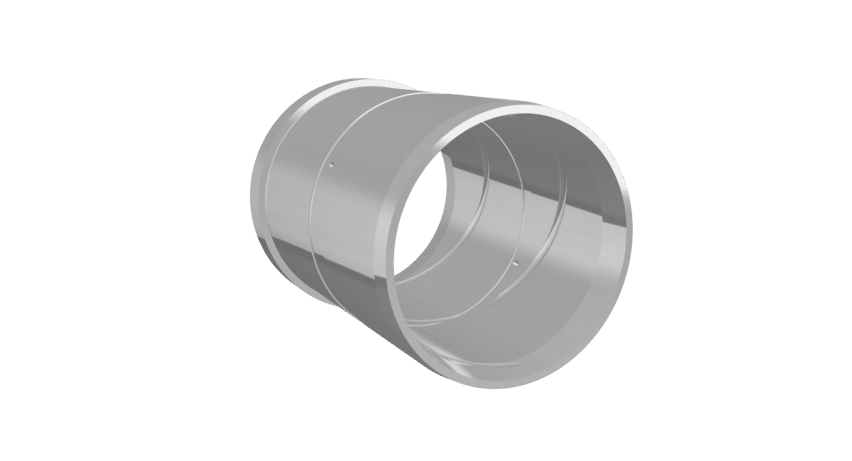
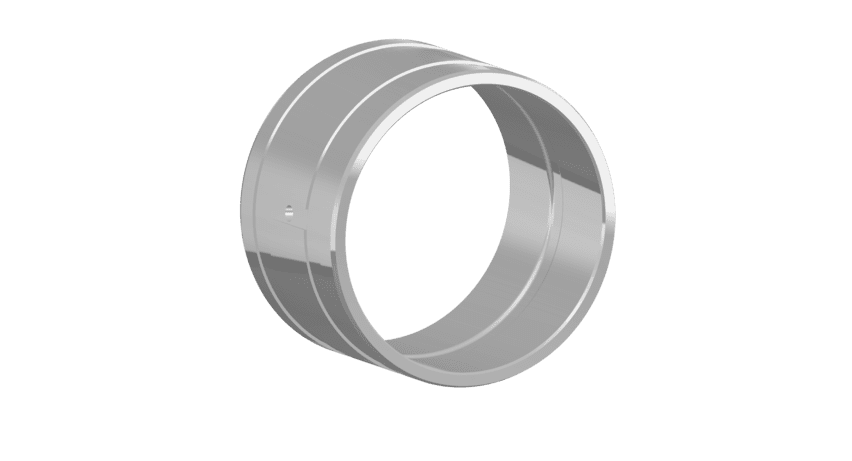
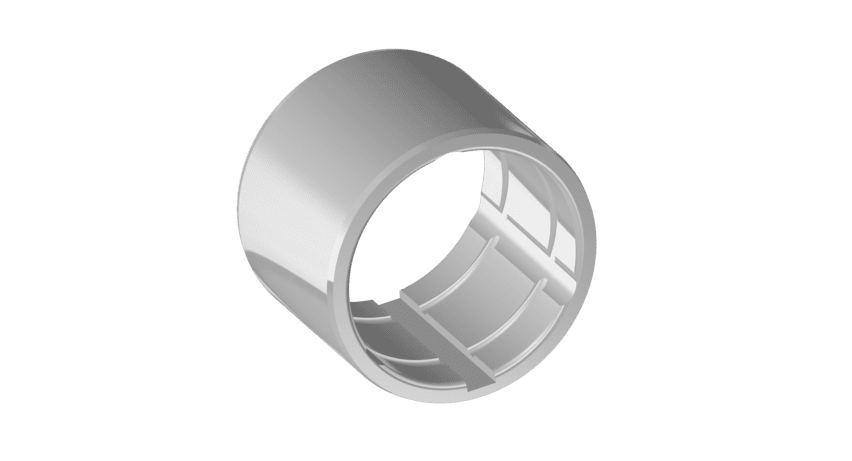

Bearing shells
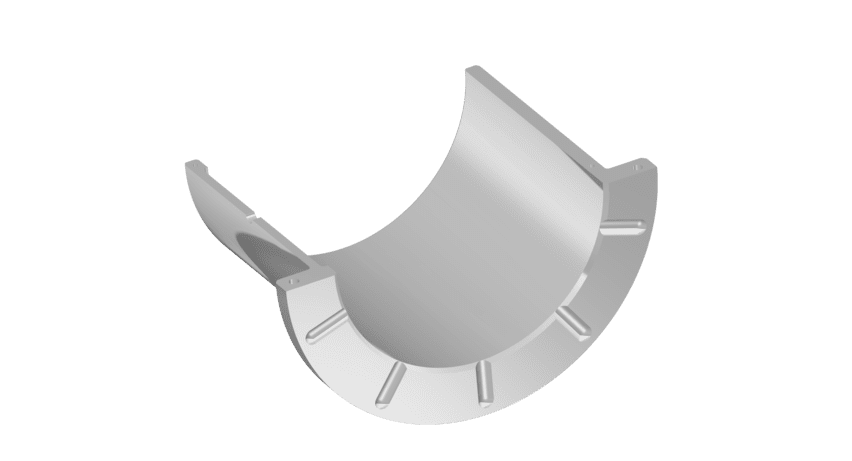
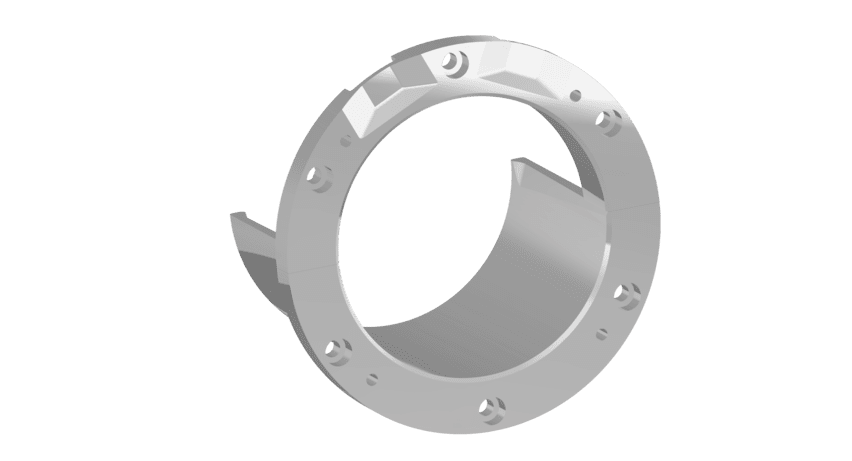
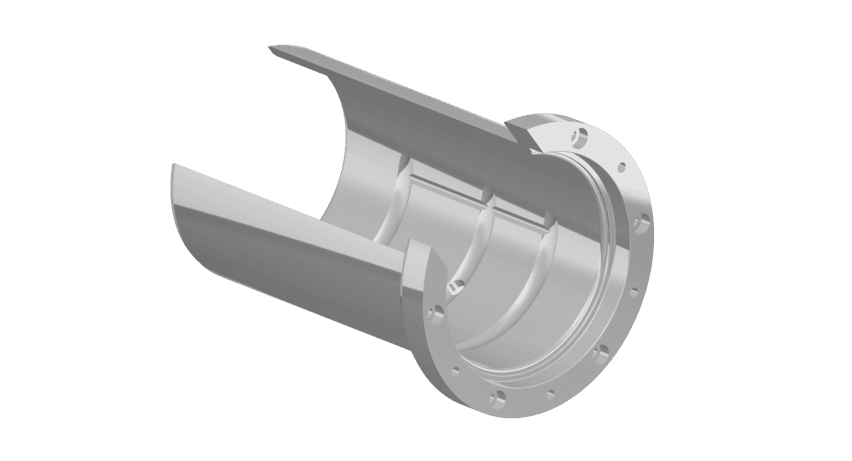
Thrust bearing
Thrust washers
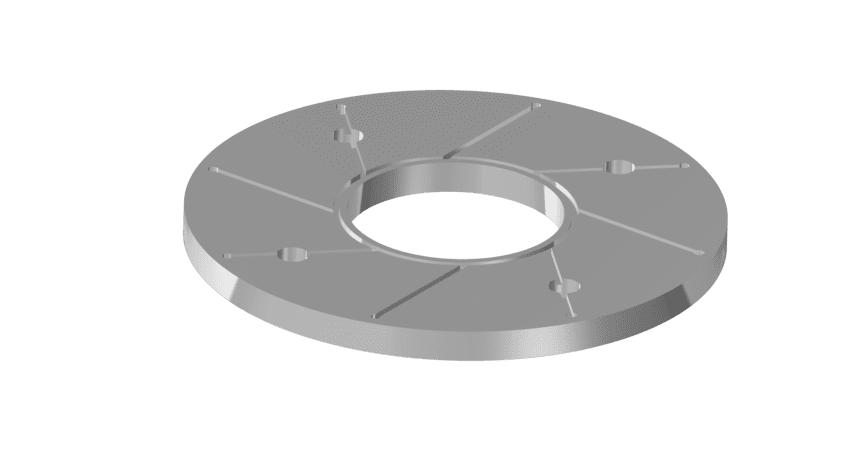