On top with green energy: voestalpine Automotive Components East London
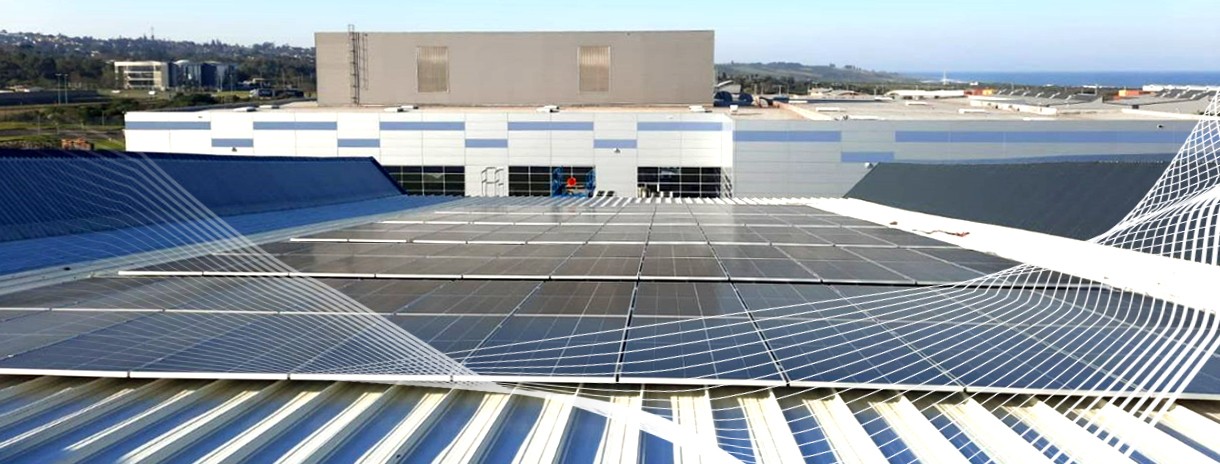
Full solar power on an area of 3,000 m²
There is no such thing as Planet B. Climate-neutral production is therefore the goal of the entire voestalpine Metal Forming Division. One example, which underlines the success of the divisional sustainability initiative to date CO2untdown to zero, is the Automotive Components company in East London, South Africa. Here, the supply of green electricity and more is already top notch.
The specialist for cold forming and complex assemblies of body and crash-relevant vehicle parts already obtains up to three quarters of its total annual electricity requirements from its own environmentally friendly production.
The photovoltaic system with 1,200 x 550 W solar cells with a peak output of 600 kWp ensures this. However, the system with its four connected 150 kW hybrid inverters, and two 700kWh lithium batteries totaling 1400 kWh does even more. As the South African state electricity supplier carries out scheduled load shedding due to severe energy shortages. Entire regions and districts of the major cities are taken off the grid several times a day, depending on the stability of the national grid. Although load shedding is supposed to run according to a schedule, this sometimes changes at minute’s notice, not enough time to bring an entire facility to a controlled stop.
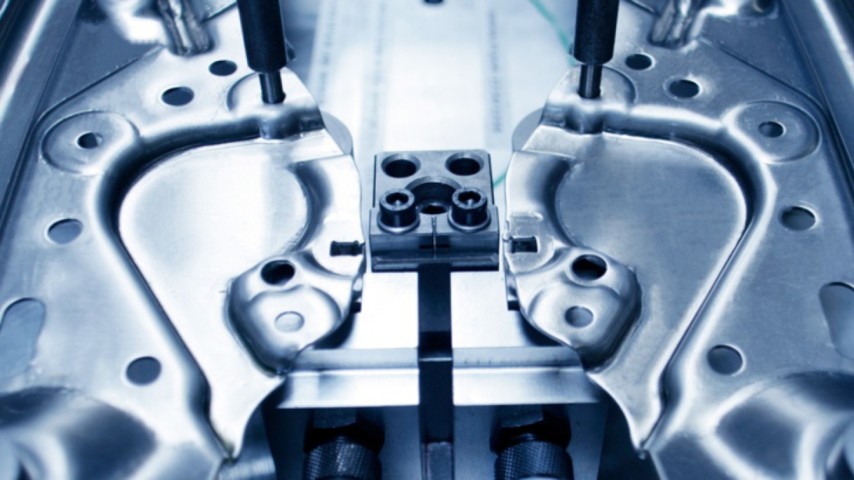
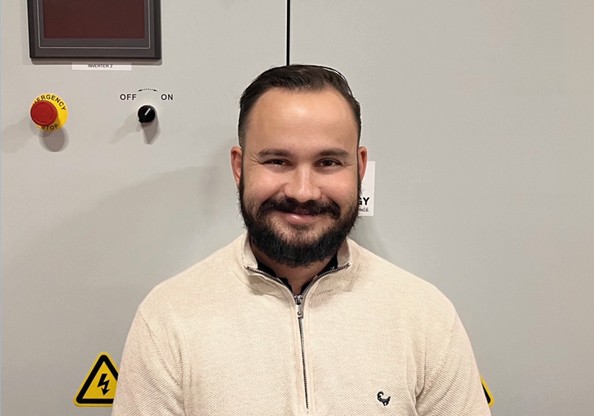
Sustainably supplied
"The entire installation of a hybrid PV solution in a body shop environment was extremely challenging. Power quality from the grid especially during switching of load shedding blocks become a problem. Our production can now continue even during government power cuts or bouts of poor quality supply. The electricity from the storage system connected to the PV system secures our production during these phases. This ensures that we are a reliable sub Saharan Africa automotive JIT supplier, today, as well as tomorrow”, says Werner Hager, Head of Production.
A welding environment with close to 80 industrial robots, compressors and chillers, also have a negative effect on power factor as well as power harmonics. Over and above the hybrid installation it is of paramount importance to ensure a good foundation in the sense of power quality, the addition of correctly sized automatic power factor correctors as well as Static Var generators.
Sustainably future-oriented
Even when designing the whole concept for the plant, which went into operation in 2014, attention was paid to saving energy. LED lighting, state-of-the-art motors with variable speed control for cooling and compressed air generation, controlled start-up of the systems to avoid high voltage peaks and much more have been in place from day one. The goal of reducing 100% of Scope 1 and Scope 2 emissions will already be achieved next year. Green power generation, the purchase of electricity from renewable energy sources and the fact that the site does not consume any natural gas will make this possible.
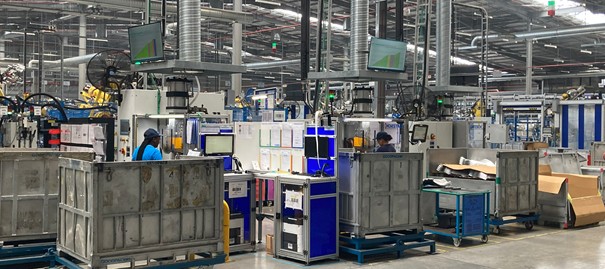
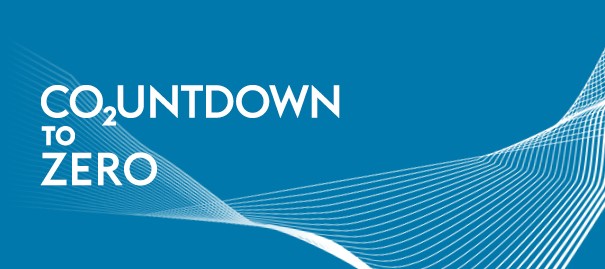
Zero CO2 as the division's target
The entire Metal Forming Division of voestalpine, which also includes the companies of the Automotive Components Business Unit, has a mission: by 2035 the entire division will produce CO2-neutrally. However, nothing works in production and administration without energy. The "CO2untdownn to Zero" concept provides clear guidelines, including: 1. save energy, 2. switch to green electricity, 3. generate renewable energy ourselves.
voestalpine Automotive Components East London shows that the direction is right.