Highly energy-efficient, sustainable progress
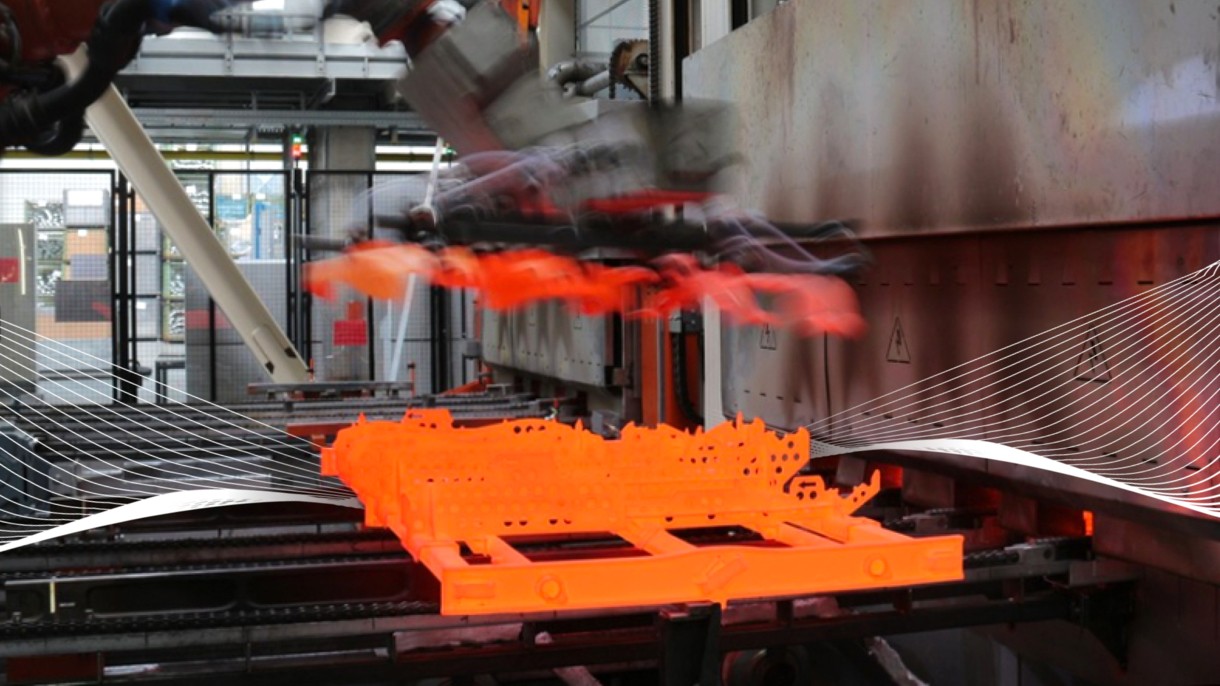
voestalpine Automotive Components Schwaebisch Gmuend
Lightweight, high-strength, corrosion-resistant - voestalpine Automotive Components Schwaebisch Gmuend has been setting standards for phs components for years. The hot forming of press hardening steel (phs) components requires high temperatures and therefore a high level of energy. With new burners and other hot possibilities, the use of energy is optimized and the CO2untdown to zero is pursued constantly.
Efficient cooperation
The innovative voestalpine phs technology enables high-strength, corrosion-resistant components to be made from galvanized steel strip. Every step must be carried out at the right time, for the right duration and at the right temperatures (up to over 900 °C). Highest component quality is the top priority. Energy and efficiency measures cannot be implemented just like that but must be precisely coordinated. Hence, all departments, from R&D, technology development and maintenance to the phs production specialists, work closely together.
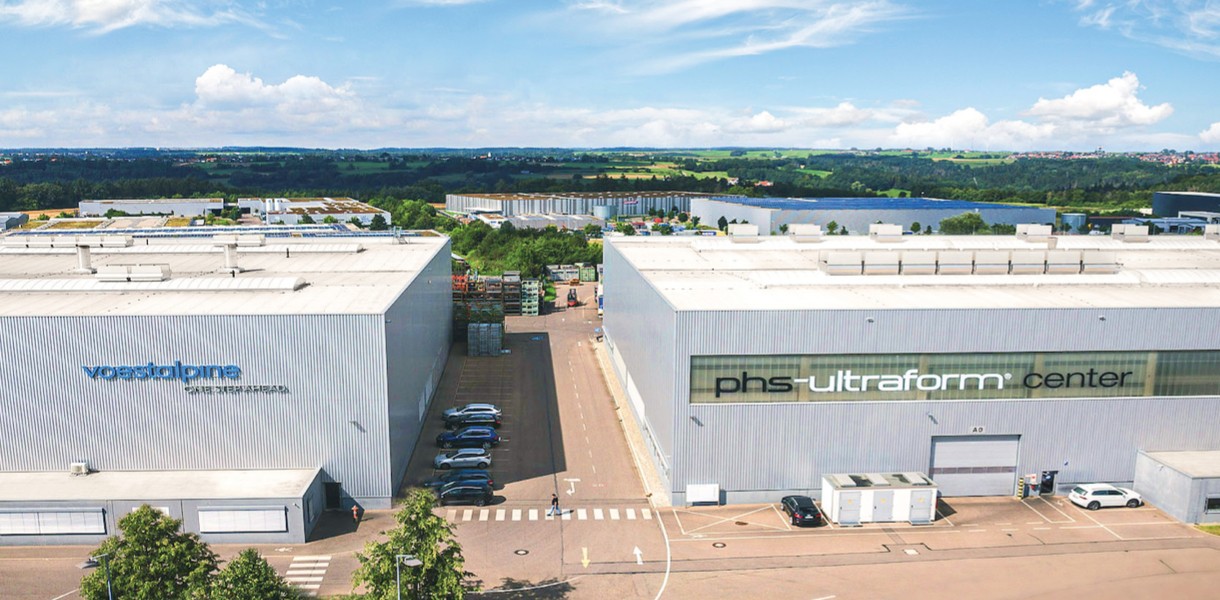
Burner with new technology
The heating up of the components is a decisive factor. It was therefore not easy to select a new burner technology, for which numerous alternatives were tested and tried out until a suitable concept for equipping the existing phs lines could be developed. Now, due to optimized flow routing an excellent heat transfer is ensured. This improved energy efficiency by more than 15 %. As a result, gas consumption and thus emissions and energy costs are reduced accordingly. In the second half of 2024, the first phs line will be fully converted to the new burner type, which will lead to a CO2 reduction of more than 200 tons of CO2 per year.
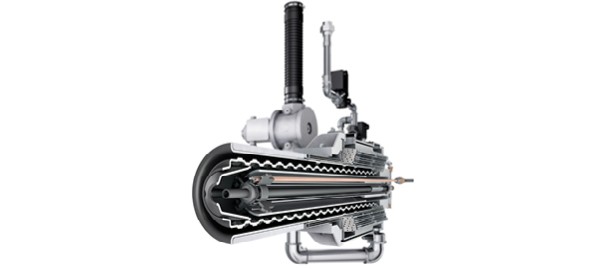
Further hot savings opportunities
The burners can be fired in any mixture ratio of natural gas and hydrogen up to pure hydrogen operation. As an electrolysis plant for hydrogen is being planned to be built in the vicinity of the plant, the phs furnaces could also be operated with emission-reduced hydrogen in the future. This would result in a further reduction in emissions.
In addition, the basis has been created for using newly designed product carriers on which the components are transported through the oven to further reduce energy consumption and thus CO2 emissions. Intensive research and ongoing tests are already underway.
CO2 – neutrality as a goal
The Metal Forming Division of the voestalpine Group, which also includes the companies in the Automotive Components Business Unit, has a mission: by 2035 the entire division will be CO2 -neutral. Even if things get hot, as they do in Schwaebisch Gmuend, the group’s competence center for hot forming, the mission will be fulfilled with know-how and commitment. Everyone is working on it. Together.