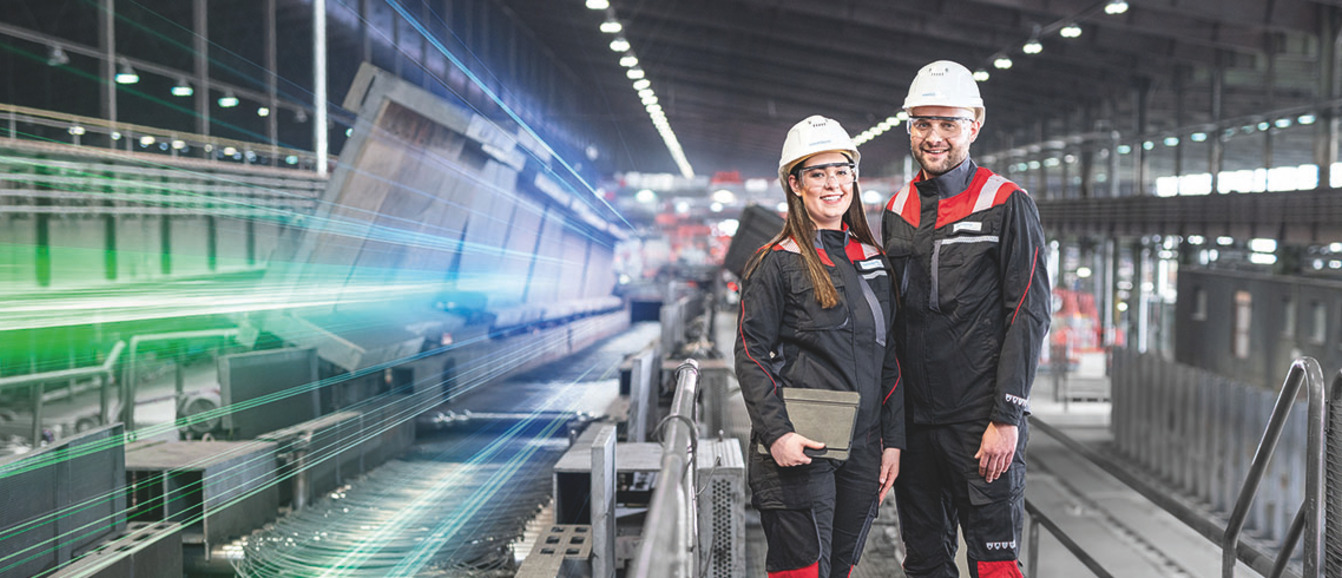
Tailor-made wire solutions
With our customized wire solutions, we meet your requirements and those of your customers. In addition to digital product simulations, our unique R&D set-up enables us to offer customized product development with significantly shorter development times. Our R&D team guarantees optimized product properties from material and process development to the drawn wire for the subsequent processing and application of your products.
Four decisive steps lead quickly and efficiently to a customized wire solution. Each step is designed to ensure the highest quality, precision and efficiency while taking into account the individual requirements and challenges of our customers.
Through a holistic approach that combines innovation, expertise and customer focus, we offer our customers tailor-made solutions for the most demanding applications.
We think holistically. In many cases, a new alloy concept is created virtually on the computer.
The products can be designed from the atomic level up to forming processes and end-properties, i.e. material simulations, process simulations, physical simulations and forming simulations can be used.
In addition, cooperation with universities and research institutes ensures access to the latest knowledge.
Unique in the world. With the MetLab and the TechMet, you have two globally unique research facilities at your disposal with which new alloys can be designed and tested on the smallest scale.
Customized chemical compositions are possible in a short time. The MetLab provides you with laboratory samples for preliminary tests from 8 kg to a maximum of 50 kg.
Based on this, individual batches can be cast in the TechMet, with which the processability is tested using a 3-ton billet in the wire rolling mill and initial customer samples are provided.
With the TechMet and the MetLab, we have installed new research facilities with which we can efficiently develop new products and materials with our customers very flexibly, on a small scale and with short time-to-market - in addition to the large-scale facilities.
The right balance. The development of our high-quality wires includes the coordination of material and surface properties.
We are also constantly optimizing wire forming in our rolling mill, in the drawing mills and at customers who process the wires into complex products.
Another focus of our development work is to generate the right balance between processing and performance properties depending on your requirements.
Customer needs dominate the systems. Our team of experts in R&D and application engineering has a deep understanding of the material properties and the physical and chemical requirements of your products.
Our own testing facilities and our extensive research network help us to overcome these challenges.
Systems tailored to customer requirements dominate the Technical Competence Center Wire. Here, material, surface and forming form a framework within which the product is further developed and optimized.
Our heat treatment capacities offer production-related conditions for simulating classic heat treatment processes for quenching and tempering. Other types of heat treatments such as Q&P and Bainitic are possible with isothermal temperature control using a salt bath.
Chamber furnace: for simple heat treatment processes without atmospheric requirements up to 1250 °C
Oil and neutral salt quenching baths: for controlled sample cooling
Retort furnace: for inert and reactive gases with comprehensive gas analysis and batch temperature control for the heat treatment of materials up to 1150 °C under closely controlled atmospheric conditions.
Application examples:
Our high-speed forming press in combination with an ultra-modern tool and die assembly makes it possible to determine the forming limit and work hardening properties of materials under the typical, demanding cold heading forming conditions.
Application examples:
The newly developed corrosion cell makes it possible to test the hydrogen sensitivity of critical alloys under simulated operating conditions, where corrosion and hydrogen diffusion play a key role in terms of product quality and service life.
Application examples:
Our test drawing line is used for targeted testing of wire rod up to 12 mm in diameter without having to interrupt the ongoing production process in the drawing shop. The drawing line is also equipped with measuring technology, such as force measurement and media monitoring.
Application examples:
A mobile RFA is available for rapid and non-destructive determination of the material composition. Mass percentages of the elements from magnesium to uranium are output. It is therefore not possible to determine the alloying element carbon using this method.
Application examples:
A fully automated coating robot is available for the optimization of surface properties, which can apply a multi-stage laboratory coating or carry out pickling and cleaning tests.
Application examples:
The thermal camera is used for mobile and contactless temperature measurement in a range from 150 to 1200°C. In addition to direct measurements, recordings (temperature and time curve) can also be made for up to 15 minutes. The software can also be used to output limit value violations via a digital signal.
Application examples:
Process & research (determination of the laying temperature at the cooling conveyor, recording of the ring cooling behavior and the temperature after the cold rolling process)
In addition to arranging and organizing standard tests and summarizing the resulting findings, our department uses the modelling and simulation facilities and materials databases within the research service company.
In addition, the department offers the conception, controlling and subsequently the data backup of projects within the R&D program:
If you have questions or feedback, please feel free to contact us. We are happy to help!