Management
Helmut LIEBMINGER
Managing Director
How can you ensure your railway assets are always in top condition? zentrak Asset and Maintenance Management provides a structured overview of your assets, enabling efficient monitoring and maintenance to optimize their performance and lifecycle.
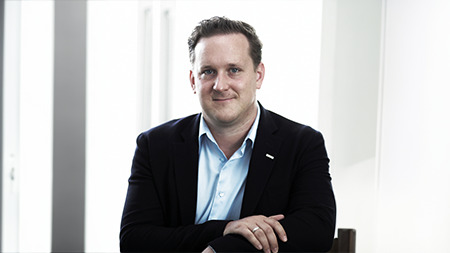
Roman BOBIK
Managing Director
By generating a digital twin of the asset, asset and maintenance data are easily accessible to the process owners and can be retrieved location independent. This data form the basis for intelligent assistance systems, ongoing process improvements and the associated optimisation of the asset lifecycle.
Terms & Conditions, Facts
-
voestalpine Digital Track Management GmbH
Waagner-Biro-Straße 84b
8020 Graz
AustriaLegal Form: Limited Liability Company (GmbH)
Registered Office: Graz
Company Registry Number: FN 563152s at the Local Court Graz
Value Added Tax-Number: ATU77438319 -
-
voestalpine DTMs philosophy and quality policy focuses on the customer. We want to add value for our customers and create partnerships based on a fair price-performance ratio. We are guided by customer specifications regarding reliability, availability, maintainability and safety (RAMS) and continuously improve our products in order to contribute to increased performance and safety of railway infrastructure. We live for open cooperation, teamwork and clear communication with suppliers and customers as well as on an internal basis.
We commit ourselves to a zero defect philosophy. This does not only apply for products but literally means zero defects in all our processes and working steps that reflected in a sophisticated quality-, environment-, occupational health and safety- as well as energy management system. We comply with legal regulations. We continuously improve quality being guided by our HSEE policy.
Skilled, motivated and result driven employees form the foundation of our enterprise. We put continuous development of our employees into the center and integrate them best possible into our processes and decisions. The optimization of our corporate image and a strengthened corporate identity support our endeavor.
-