The first steps:
Longitudinal slitting, large reel and spiral storage unit
Steel strip preparation
Productivity, efficiency and cost-effectiveness are key here once again.
The production process is continuously optimized to minimize downtimes and scrap.
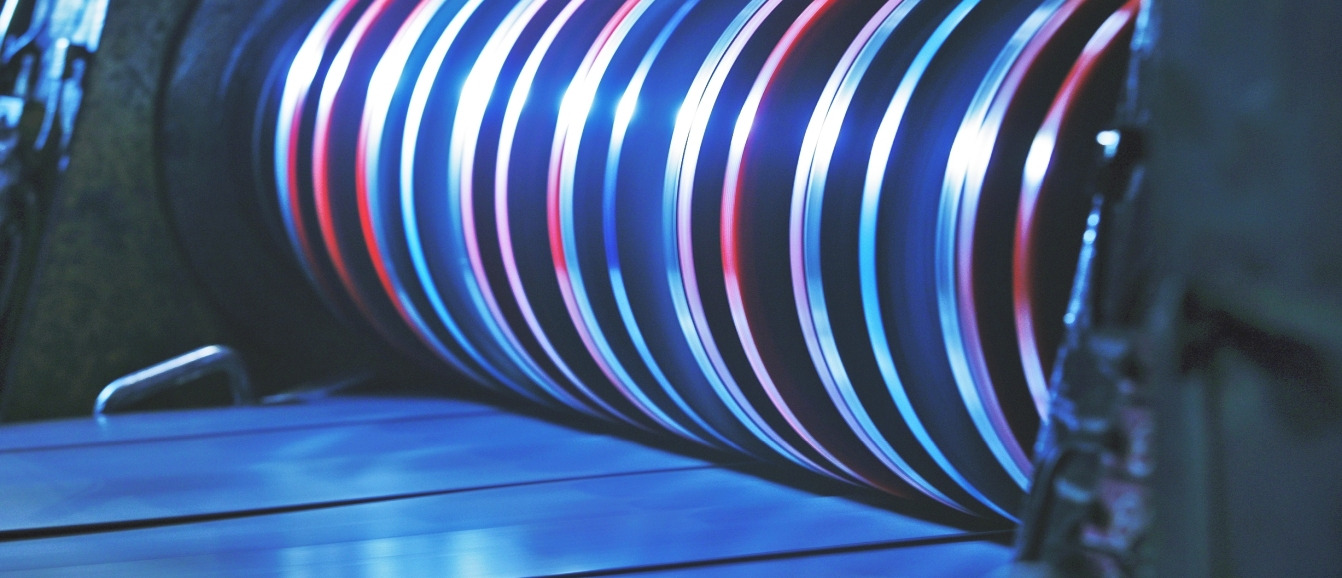
The coil is divided into strips and reeled up using a shear frame equipped with circular rotating shears. The edges are trimmed and the edge strips are shredded using scrap chippers and then disposed of via conveyor belts.
When changing over to a different strip constellation, the entire change stand with the circular shears can simply be replaced using a conversion crane. The changing frame itself is prepared in advance at a separate blade changing station.
Benefits
- Scrap goes back to voestalpine Linz and is recycled
- Max. Productivity - necessary work steps and equipment are prepared in advance, which means less downtime!
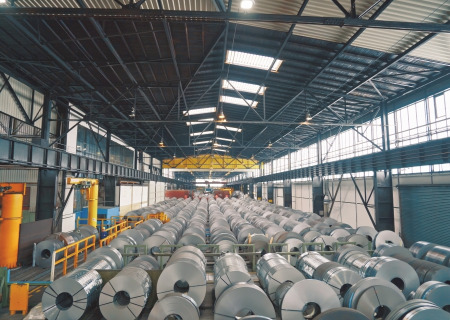
Large coiler
The slitted rings are welded together at the steel strip ends and wound into coiling cages:
- 3 - 5 rings per coiler
- Trouble-free process possible with section and hollow section systems
- Times for ancillary activities such as welding and additional scrap due to downtimes are reduced
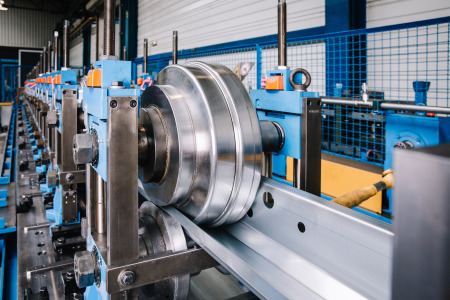
Spiral storage unit
The steel strip is stored in 4-ply loops. The strip ends are welded together independently of the system:
- No production downtime - the system retrieves the belt from the channel as required
- Minimization of ancillary activities - parallel working
- Scrap reduction
Tomorrow's topics that are already of relevance to you and us today: