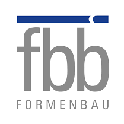
In addition to the basic technical function of a moulded plastic part, aesthetic aspects in particular play a decisive role in today’s purchasing decisions. In the case of housing components – such as this demonstrator – non-optimised thermal management of the mould insert can not only lead to dimensional deviations, but also to visible weld lines and flow lines in the area of functional elements and openings. This often results in higher reject rates and longer cycle times due to process-related corrective measures.
Customers often associate quality and durability with the external appearance of a product Surface textures can convey a certain value and strengthen customer loyalty. In addition to the aesthetic aspects, the finest textures can also increase product protection. In the future, hidden codes in the texture will play an increasingly important role. These codes can not only ensure protection against counterfeiting, but also provide customers with additional product information.
Meeting the diverse requirements and boundary conditions for highly complex molded parts requires precise interaction and fine-tuning of the individual disciplines. The demonstrator on show illustrates the potential that can be tapped by combining state-of-the-art design methods, production technologies and materials.
AM-POWDER (premium material from BÖHLER and UDDEHOLM)
Our long history of developing materials for the die casting industry means that the powders we use are of the highest quality and offer superior tool life. Our AM powders are developed and manufactured by the same experts who are responsible for our first-class tool steels.
Uddeholm Corrax® for AM and BÖHLER M789 AMPO | Uddeholm Corrax® for AM and BÖHLER M789 AMPO |
---|---|
Developed for tool applications that require corrosion resistanceRecommended hardness from 45 to 52 HRCHigh corrosion resistance | Developed for highly demanding applications in toolmaking such as reinforced plasticsRecommended hardness in use 48 – 57 HRCHigh toughness |
Material | Achievable | corrosion resistance | Wear resistance | Polishability | Notched impact strength 6 [J] |
---|---|---|---|---|---|
1.2083 ESU | Hardness1 | « | ««« | «««« | / |
Uddeholm Corrax® for AM | 52 HRC | ««««« | ««« | ««««« | «««« |
BÖHLER M789 AMPO | 50 HRC | ««««« | ««« | ««««« | «««« |
1.2343 ESU | 52 HRC | / | ««« | ««««« | / |
BÖHLER W722 AMPO (~1.2709) | 53 HRC | / | ««« | «««« | / |
Uddeholm Dievar® for AM | 54 HRC | / | ««« | ««««« | ««««« |
BÖHLER W360 AMPO | 53 HRC | / | ««««« | «««« | ««« |
The design of tools for additive manufacturing and process simulation go hand in hand. Our AM experts create comprehensive computer models to identify potential failure modes and eliminate these problem areas. Our experts also ensure that the potential of additive manufacturing is fully utilised. This guarantees that the best possible design solution is chosen before we print the part.
The conventional cooling channel layout requires higher mould temperatures in order to minimise the visual appearance of weld lines and flow lines. However, this is accompanied by an increase in cycle time and the reject rate due to optical defects cannot be completely avoided. However, this is accompanied by an increase in cycle time and the reject rate due to optical defects cannot be completely avoided. Process parameters and mechanical loads were analysed in order to create a detailed digital twin of the injection moulding process for the housing. Thanks to the optimised temperature control, reject rates were eliminated by avoiding flow lines and surface defects.
In general, conformal cooling channel concepts can follow the complex contours of the mould and ensure uniform heat extraction compared to conventionally drilled cooling channels. This consistency guarantees uniform temperatures across the tool surface, eliminates hot spots and minimises thermal stresses. Close contour cooling channels have the potential to significantly reduce cooling times and thus increase production efficiency. In addition, the close contour design enables superior component quality by minimising distortion and defects.
The near-contour cooling design in the demonstrator was also optimised for variothermal process control. By increasing the heating surface and minimizing the distance between the cooling channels and the tool wall, extremely rapid heating of the tool wall was possible. This eliminates visible flow lines on the surface of the component and enables the imaging of fine surface structures such as the holograms shown here. During the holding and cooling phase, the conformal layout enabled faster cooling of the component compared to the conventional structure. This meant that a defect-free component could be produced with a shortened cycle time.
Variothermal temperature control of injection molding tools improves the aesthetic properties of injection molding structures compared to conventional injection molding by adjusting the mold temperature. In contrast to conventional injection molding processes, in which the molten plastic immediately forms a frozen surface layer upon contact with the mold wall, in the variothermal process the temperature of the mold wall is increased before injection and only cooled after the filling process. This prevents the surface layer from immediately freezing, improves the level of gloss, shapes surface structures more precisely and the viscosity remains constant throughout the entire injection phase. For the economical use of variothermal temperature control, the temperature-controlled tool volume must be kept as small as possible in order to ensure efficient and rapid heat supply and removal.
The conformal temperature control channel layout in conjunction with the variothermal temperature control was analyzed numerically in collaboration with our cooperation partner SIMMO GmbH.
The great potential of near-contour temperature control in conjunction with variothermal process control has already been demonstrated and optimised. At a flow temperature of 120/60 °C, the mould insert can be heated from 62 °C to 116 °C within 11 seconds.
We ensure the highest possible quality, reliability and consistency of additively manufactured components by controlling every step of the value chain from powder production to delivery. Whether it’s a single part order or series production, our internal quality systems ensure that we fulfil your requirements every time. We use state-of-the-art tools to continuously improve and refine our internal printing processes. Design of experiments, statistical process control and process monitoring form the basis of our methodology. The continuous innovation of our AM and material groups ensures that we deliver superior material properties for the most demanding applications. The result is that our customers can put the parts into operation with maximum confidence.
We understand the interactions between laser and material. This in-depth understanding of AM and PIM enables our customers to create added value for their company and achieve competitive advantages.
Picture left: Tool insert de-powdered
Our post-processing options range from the simple separation of the component from the building platform to the removal of powder from cooling channels close to the contour to the ready-to-install product. Our vacuum hardening shops are equipped with vacuum hardening furnaces of different sizes and therefore offer a high degree of flexibility in hardening and tempering. Thanks to the expertise and many years of experience of our specialists, we can ensure optimum heat treatment results and reproducible properties for our additively manufactured components.
We understand the interactions between the additive manufacturing process and the material and, thanks to this in-depth understanding, enable a process-reliable solution and a non-porous surface for the highest component surface quality.
Left: “Build Zone” of the optimisation target, determined by process monitoring with EOSTATE Exposure OT (top) and EOSTATE MeltPool (bottom).
Centre: Experimental design for parameter optimisation using the contour mapping of the reaction surface design for porosity (top) and the corresponding metallographic sample after optimisation (bottom).
Right: Microstructure of the AM-processed H13 type, analysed by SEM (top) and EBSD (bottom).
The machining of the near-contour insert was carried out by the cooperation partner FBB Formenbau Buchen GmbH. This forms the basis for all downstream processing steps.
FBB is an experienced expert in the manufacture of plastic and silicone products, developing customised tools and moulds in line with customer requirements and quality standards. Whether for injection moulding or silicone injection moulding, FBB is your reliable partner for high-quality and functional products in professional and private environments.
Picture left: Mould insert after die sinking
Polishability is an extremely important factor in the plastic injection moulding industry. The polishability of additively manufactured moulded parts depends on a number of factors such as the printing parameters and the quality of the powder. We have optimised our printing and powder manufacturing processes to ensure that our printed inserts can be polished to meet SPI industry standards. Close co-operation between parameter development and our polishing experts at the voestalpine eifeler group of companies enables us to achieve the highest quality polishing results through the use of innovative technologies and polishing processes
The processing parameters optimised for our own powders ensure that the components are non-porous (density 99.98 %) and enable high-gloss polishing (SPI-A1)
Highly polished tool insert
High-gloss polished surface
Mirror-smooth surface
Eschmann Textures offers a wide range of technologies worldwide for the surface treatment of plastic processing tools according to individual customer requirements. Depending on the specific tool geometry and design requirements, we always provide the appropriate technology for subsequent tool processing. To do this, we draw on a diverse production portfolio that includes high-precision 5-axis laser processing and classic etching technology. In this way, we open up new perspectives for plastic moulding tools by creating appealing visual and tactile surface textures that range from automotive applications to lifestyle products.
The tool insert is provided with a background texture into which a digital watermark has been integrated. The femto laser technology used means that even the finest structures can be applied.
Digital watermarks can be used to integrate invisible information into the surface of plastic products. We have integrated the digital watermark into the laser structuring of the case surface. Possible uses of this technology include efficient tracking of content, increasing consumer interaction and maintaining brand reputation. Furthermore, the technology for integrating recycling information directly into the component surface may become increasingly important in the future.
Using the demonstrator as an example, you could follow the watermark directly to this website. Eschmann Textures is your partner for the integration of digital watermarks in moulds for plastics processing.
Here is the link to the Digimarc app
The flame-retardant PC/ABS moulding compound used for the housing makes it necessary to protect the fine hologram texture against wear in order to maintain the effect over the service life of the mould. The required wear resistance of the surfaces while maintaining the high-gloss surface is achieved with the TiN-ultrafine coating from voestalpine eifeler Coating. In addition to wear protection, the coating also has a positive effect on demoulding.
With its advanced services, technologies and products, voestalpine eifeler Coating has been offering targeted adjustments to surface properties for over 40 years, thereby enabling the optimisation of manufacturing processes and tool properties. The right product solution for the respective customer application reduces wear and increases the service life of tools and components.
Thanks to our femto laser technology, extremely precise fine structures can be incorporated into the tool surface, such as our hologram effects, for example, which are used to create the “voestalpine – one step ahead” lettering. These structures utilise the phenomenon of diffraction, in which light waves that hit the structure spread out instead of being reflected in one direction only. Depending on the position of the observer and the light source, the light is refracted in different spectral colours.
This effect can be reproduced on the surface of the moulded part in the injection moulding process and not only serves an optical purpose, but can also be used for safety applications.
The mould insert was inspected by the cooperation partner FBB Formenbau Buchen GmbH. Both the conventionally drilled insert with continuous water temperature control (90 °C) and the additively manufactured insert with near-contour, variothermal temperature control (70/140 °C) were sampled. Due to the increased flow front temperature in the variothermal process, the flow lines could be completely eliminated.
The near-contour cooling channel layout enabled the mould insert to be heated to the target temperature of 120 °C very quickly. This meant that heating could be achieved during off-peak times. The lower mould temperature in the holding pressure phase and residual cooling time made it possible to reduce the cycle time by 18 %.
Our patented technology for integrating thermocouples into additively manufactured mould inserts enables extremely precise placement of the measuring points directly below the mould wall. We utilise the greater design freedom of additive manufacturing to integrate the sensors without compromising the layout of the temperature control channels. There are many possible applications for this technology. They range from monitoring the mould temperature to analysing the functioning of cooling channels over a certain period of time. Potential faults in the temperature control system can also be detected. In this demonstrator, the variothermal process control is recorded quantitatively. Process monitoring systems such as ComoNeo from our co-operation partner, the Kistler Group, can be used to carry out these tasks.
Two thermocouples are integrated in the demonstrator shown. One sensor measures the cavity temperature in the area of the flow line, the other in the area of the hologram structure. With the help of these sensors, the heating and cooling phases in the areas of flow line formation and the hologram structure could be quantitatively recorded. This provided insights into the process that can be used both to improve component quality and to optimise the cycle time. Thanks to the precise positioning of the thermocouples, the heating and cooling phases could be recorded without any time delay compared to the measurement of the return temperature. This enabled the variothermal injection moulding process to be efficiently optimised in terms of cycle time.