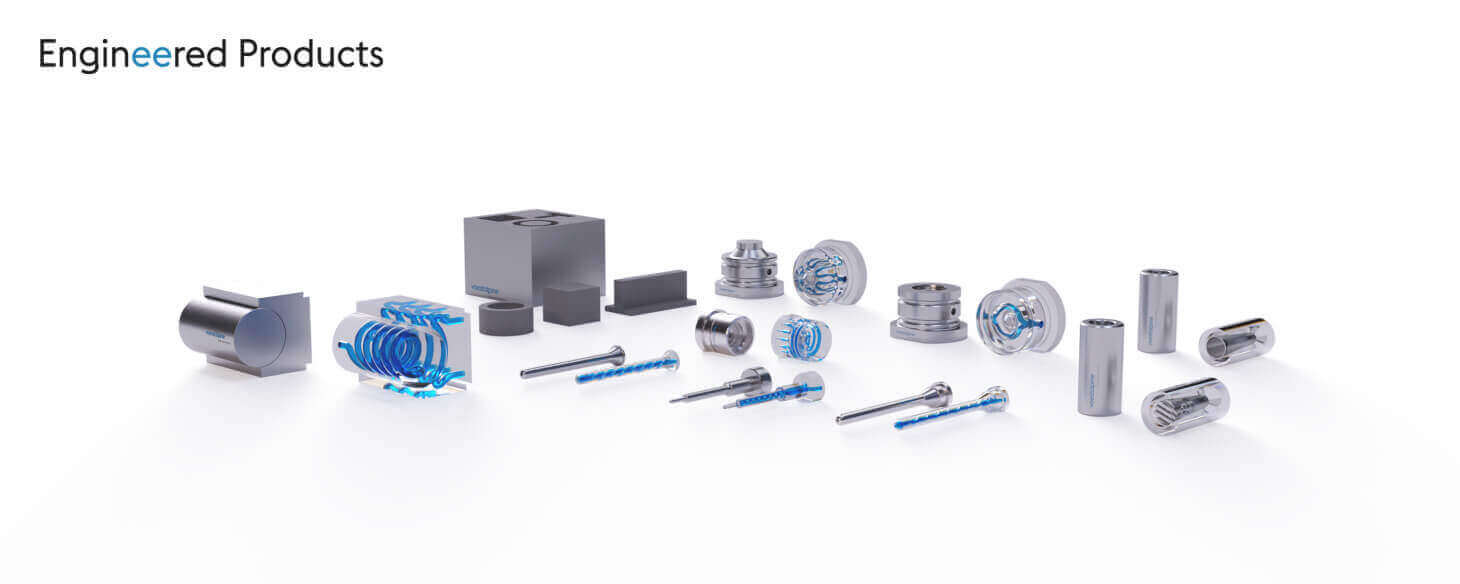
In this article, we explore how injection molders can eliminate flow lines in their parts through the efficient use of optimized variothermal conformal cooling design. We compare the costs and benefits of the optimized voestalpine conformal cooling solution against a conventionally cooled alternative. The savings alone are impressive:
Our analysis also demonstrates that the voestalpine solution can not only enhance part quality and reduce costs, but it can also significantly expand design possibilities. By using the voestalpine solution, injection molders can overcome production challenges and meet the growing demand for high-quality, aesthetically appealing plastic parts.
To showcase voestalpine HPM solutions for plastic injection molding at the 28th Fakuma trade fair in Friedrichshafen, Germany, we developed a cavity insert for an electrical housing cover. The cavity insert and produced plastic housing cover demonstrated our seamless value chain—from concept to finished product. Alongside our project partners, our experts highlighted the many state-of-the-art design features and the added value for customers to the trade fair visitors. You can read more about the voestalpine cavity insert and produced plastic part here, which is also the subject of our cost comparison in this article.
We designed the electronic housing cover showcased at Fakuma to meet the highest technical demands and aesthetic functions. The technical design was primarily determined by the high requirements in terms of protection against dust and water (IP66/67), impact resistance (IK08) and flame retardancy. This resulted in high wall-thickness variations (0.7 to 4.5 mm) and unique features such as screw bosses and sealing grooves. The processing of the flame-retardant material (PC-ABS + FR) in combination with the geometric properties and the high-gloss surface on the visible side also required precise process control to ensure high article quality and reproducibility.
When using molds with conventionally drilled cooling channels, it is only possible to reduce the visibility of flow lines by adjusting parameters in the injection molding process—such as maximizing holding pressure and cavity wall or melt temperature—but it is not possible to eliminate flow lines completely (see Figure 1). The downside of these adjustments, particularly higher temperatures, is the significant increase in the cycle time, leading to reduced efficiency and higher costs per plastic part. In the case presented, the cycle time increased to 77.9 seconds due to an extended cooling time of 67.3 seconds.
To eliminate flow lines, variothermal process control can be used to delay the solidification of the melt on the cavity wall by heating the mold before injection. This allows sufficient fusion of the flow fronts and reduces the visibility of the flow lines. One disadvantage of variothermal temperature control, however, is an increase in the cycle time due to additional heating times and longer cooling phases. Increased energy consumption is also associated with this.
Figure 2 compares the different temperature control concepts and their effects on the resulting cycle time. To eliminate flow lines for the PC-ABS molding compound, a cavity temperature of 130 °C is required during injection. On the left, the 54% increase in cycle time can be seen, which is necessary with a conventional gun-drilled cooling layout to realize variothermal process control and to eliminate the flow lines.
Compared to the conventional cooling layout, considerable savings can be achieved with conformal cooling (images center and right in Figure 2 below). Further information about the conformal cooling design can be found here in section 2. Due to the small and even distance between the cooling channels and the cavity insert surface, conformal cooling offers two decisive advantages over conventional temperature control:
The injection molding tests of the variant with one-sided conformal cooling only on the visible part side (Figure 2 center) show that up to 47% cycle time can be saved compared to conventional cooling. It is quite remarkable that, despite the variothermal temperature control, the cycle time of the one-sided conformal cooling design can be reduced by 18% compared to conventional cooling design with isothermal process control; and the flow lines can be eliminated at the same time. One reason for this is the parallel conformal cooling channel design that ensures high flow rates as well as low pressure drop and the avoidance of riser cooling. If both sides are conformally cooled and variothermally tempered, the cycle time can even be reduced by 58% (Figure 2 right).
Looking at the process costs in Table 1 (below) of the three variants shown in Figure 2, the part costs are primarily determined by the machine and energy costs. By reducing the cycle time, considerable savings in part costs of 37% or 42% are possible by using one- or two-sided conformal cooling. However, the cost savings are also offset by the additional insert costs of 4,000 € (one-side AM) or 7,000 € (two-side-AM) using additive manufacturing compared to conventional manufacturing.
Figure 3 (below) shows that the return on investment, including the additional costs of the AM-inserts, is achieved quickly. For the one-side AM variant, the break-even point is reached after 3,376 shots; and for the two-side AM variant, after 5,238 shots. If the two AM variants are compared with each other, the two-side AM solution is economical after 20,377 shots.
The potential cost savings are not determined by the cycle time alone. Sufficient part quality in terms of surface finish and part tolerances (ensuring IP and IK protection classes) must also be guaranteed to keep scrap rates to a minimum. The part tolerances are mainly determined by the warpage. As shown in Table 2 below, by means of conformal cooling, warpage was reduced by 7,5% and 61%, thus improving part tolerances and minimizing the scrap rate to 3% and 1%. So, the break-even-point for the AM-inserts can be attained nearly 10% quicker.
It is noteworthy that the part warpage with the two conformal cooling designs can also be reduced compared to initial conventional cooling (see Figure 1) using isothermal temperature control (0.583 mm): for the one-sided conformal cooling solution by 3.8% and for the two-sided solution by 59%.
This case study and cost comparison clearly shows that the combination of variothermal temperature control and the optimal conformal cooling design is a win for the injection molding industry. The higher investment costs for a superior cooling channel layout pay off after less than 6,000 shots. Compared to the lifetime of this injection mold of 500,000 shots the savings are 740 k€ and the additional costs of the additively manufactured inserts are balanced out by the savings after 3 days!
Would you like to find out more about the cost-effective elimination of flow lines or a similar challenge in your business? Our friendly experts are ready to speak with you. You can contact them using the button below.
Ready to learn more about how voestalpine HPM is helping our customers in the plastic processing industry? Check out our recent articles below. You will also find our page about voestalpine Engineered Products for Plastic Injection Molding directly below or by clicking here.