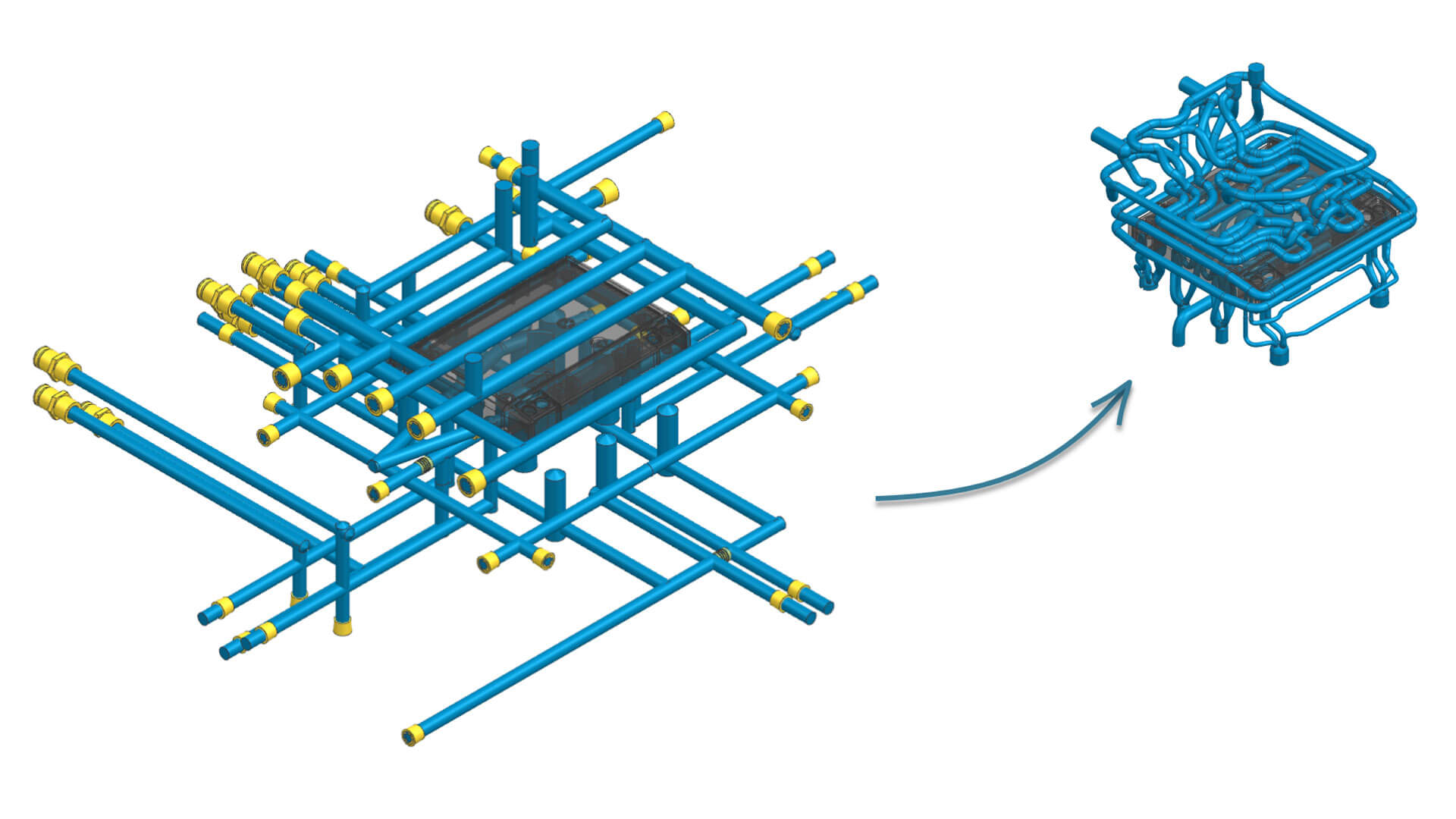
With the introduction of voestalpine Sensorized Inserts, plastic injection molders can now look forward to a significant advancement in their process monitoring and control to ensure consistently high part quality. As part of the voestalpine Engineered Products range, these inserts offer greater design freedom by overcoming conventional positioning constraints, such as those caused by cooling channels or ejectors, which may have previously limited process insights even with advanced measurement technology.
voestalpine Sensorized Inserts enable the seamless integration of internal channels for sensor placement via additive manufacturing (AM). Through our integration know-how, small diameters can be realized with accurate positioning as close as 0.5 mm from the cavity. This allows precise process monitoring at critical areas of the plastic part, such as thick wall sections or flow lines, without sacrificing cooling performance.
AM design freedom allows the sensors to be optimally positioned between the cooling channels and cavity wall, eliminating the need for additional drilling. Moreover, conventional thermocouples offer a cost-effective alternative, as they can be installed directly into the mold insert.
You can find out more about the technology behind the sensorized inserts and how they can be integrated into your production chain by reading out blog post: Trends in plastic injection molding: Sensorized inserts .
Designed to increase production efficiency and plastic part quality, the sensorized inserts offer the following benefits:
Plastic injection molders can integrate these sensorized inserts for several use cases:
Process monitoring is used to save time in process set-up and to monitor critical part features, ensuring consistently high part quality. With voestalpine Sensorized Inserts the cavity-wall temperature profile of multi-cavity molds can be monitored.
The blockage of cooling channels in a multi-cavity tool can lead to increased scrap rates. Its detection via the flow meter is delayed, and without additional investigations, it is not possible to predict which cavities are affected. Compared to the flow rate decrease, the temperature increase in the cooling channels is instantly detected, allowing allocation to the specific channel.
The set-up and optimization of variothermal injection molding processes is time-consuming and unstable due to process conditions. Thus, the switch-over between heating and cooling can be reproduced using a temperature sensor at the quality-determining points, e.g., flow lines, without negatively affecting the cooling channel layout.
You can find out more about varothermal processes by reading our recent blog article here.
You can find out more about voestalpine Sensorized Inserts by visiting the new product page here (LINK). You will also find a product datasheet on the product page.
You can find out more about voestalpine Engineered Products for Plastic Injection Molding on our overview page here.
Our friendly experts are also ready to help you further. You can contact them below.
Find out more about how voestalpine HPM is helping our customers in the plastic processing industry. Explore our recent blog articles below: