If something needs to be shaped, our expertise in tools is called upon. From the production of high-quality tool steels to their distribution, our voestalpine companies control the entire supply chain. As one of the world’s leading suppliers, our range of products includes:
- tool steel and high-speed steel;
- tools for hot and cold forming;
- valve steel;
- powder metallurgically produced steels;
- special steels and nickel-based alloys;
- additively (3D) manufactured pre-material and tools; as well as
- drop forge parts made of titanium alloys, nickel-based alloys, as well as high, medium, and low-grade alloyed steels.
Each tool application has its own specific needs and requirements. We perfect individual tool solutions for them. The selection or development of the optimum steel is just as much a part of this as the appropriate heat treatments, coatings, or additive manufacturing. Discover our product portfolio:
High-performance materials
When it comes to steels for the tool industry, it all comes down to the optimum formulation as well as the right manufacturing and processing expertise. We develop suitable alloys and treatment concepts for every application.
We adapt precisely to the wishes of our customers and their requirements when manufacturing the respective steel grades.
-
Drills, milling cutters, broaches—these are the mechanical tools that probably first spring to mind when you hear the word “tool.” The steel they are made from is known as high-speed steel. We give it a special hardness so that it can cope with the challenging task of machining. However, hardness is not the only factor. High processing speeds give rise to high temperatures. To withstand these, our high-speed steels have an extraordinary hot hardness and are also particularly hard-wearing to extend the interval between tool changes. Ultimately, the toughness of these steels prevents the cutting edges from breaking off.
From our production sites in Sweden, Brazil, and Austria, we supply customers with high-speed steels tailored to their requirements. With our extensive range of high-speed steels produced by powder metallurgy, we can meet the most demanding requirements, particularly in terms of wear resistance and corrosion resistance.
-
Hard-wearing and resistant to corrosion: Cold work tool steels also have to stand up to these challenges. No premature chipping, cracking, or plastic deformation is allowed to interfere with the reliable use of tools made from these steels. The term “cold” for these steel grades refers to their use in conditions around room temperature. However, the heat from friction and the pre-material can raise them to a working temperature of approx. 250 °C.
Heating up and cooling down—this characterizes a supplement to cold forming that is becoming increasingly important, especially in the automotive industry. During press hardening, the forming tools made from our tool steels withstand special requirements. Their high thermal conductivity combined with high toughness allows hot sheets to be efficiently shaped and at the same time radically cooled to achieve high strength. This reduces production costs and allows the component’s weight to be reduced by around a third.
In the area of “classic” cold forming, our cold work tool steels are used to produce tools for
- pressing;
- cutting;
- punching;
- extruding; and
- embossing.
Wear resistance, even in the smallest detail, is one of the most important properties. Since non-metallic inclusions in the steel would have a detrimental effect on tool performance and service life, particularly given the delicate nature of this work, we use manufacturing processes that enable maximum purity. These include, for example, powder metallurgy and electroslag remelting.
-
Things get hot when using hot work tool steels. The tools that are made from them have to hold workpieces at a temperature of around 400 to 1,200 °C during forging, die casting, or extrusion, for example. We therefore ensure that our steels are extremely heat-resistant and can withstand permanent changes in temperature.
The areas of application for hot work tool steels are considered to be especially demanding when it comes to tool steel. They exhibit problems such as
- hot wear;
- thermal fatigue;
- crack formation; and
- plastic deformation.
Our expertise enables us to provide our customers with steels that have a particularly stable, heat-resistant structure. Using them means that the intervals between tool replacement can be significantly extended.
We meet the current development trends, e.g., producing higher quantities of ever larger die-cast parts in the automotive industry, with large-scale tool steel blocks. Their often complicated structures, coupled with high demands on the surface, require die-casting tools made from steel blocks weighing around 18 tons, which our production companies are able to manufacture.
-
Plastic molding tool steels are used to produce the molds and dies required for the manufacture of plastic products: from attractive packaging to highly sensitive cell phone displays and medical technology products.
The efficient shaping of plastics requires the tool steel to have unique properties: corrosion and wear resistance, toughness, and polishability. The plastic molding tool steels developed by us have proven themselves in the production of millimeter-small lens systems for smartphone cameras, among other things.
The production of plastic components from sustainable raw materials involves higher risks of problems such as corrosion and wear for the molding steels used. A distinction is made here between biodegradable plastics and bio-based plastics, as they differ in terms of their properties and areas of application.
-
Plastic molding tool steel for highly polishable tools is one of our particular specialties. For example, light guide plates are manufactured in molds made from this high-quality material. These plastic panels convert the light from a spot or linear LED into an area light. They ensure uniform backlighting and a bright picture in smartphones, tablet PCs, and LED TVs.
Our steel gets its extreme polishability from its uniform structure. The cleaner the steel for these applications, the better the results. Irregularities, inclusions, or even cavities are unwanted. Our material experts developed a new steel formulation for this. In conjunction with a modified production process, they created the conditions for high-purity, corrosion-resistant, and highly polishable plastic molding tool steel. It consists of a precisely balanced alloy and benefits above all from a small amount of nitrogen, which improves corrosion resistance and supports the uniform structure.
Special areas for our tools
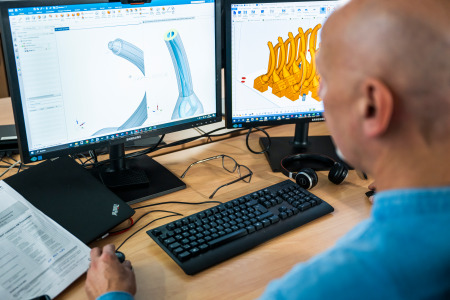
The requirements in tool and mold making are constantly increasing in the areas of die casting and plastic injection molding—and so is the number of solutions for our customers. In die casting, the focus is on the production of larger components and the realization of thinner wall thicknesses. In plastic injection molding, on the other hand, the demands on the surface quality of the molded part and the component tolerances are increasing. Based on voestalpine’s expertise in the field of materials for the tool industry, we are expanding our range of products and services for this sector.
-
Thanks to our many years of global experience in the die casting and injection molding industries, we know that lower rejection rates, optimized cycle times, lower maintenance requirements, and a longer mold service life are key challenges in these sectors. Engineered products are developed to solve them.
We design and manufacture these ready-to-use and customized components from voestalpine premium materials in continuous internal production chains so as to meet the highest customer requirements.
Our engineered products for die casting and plastic injection molding are produced either in the
- conventional method or through
- additive manufacturing
and enable higher productivity and lower total cost of ownership per molded part. Thanks to their outstanding technical properties and long service life, they ensure higher part quality and contribute to a reduction in rejects, maintenance, and machine downtime. By using additive manufacturing technologies in combination with our high-quality powder materials and our engineering expertise, the cycle time of your processes can also be reduced by means of conformal cooling. Improved temperature control also enables tighter component tolerances thanks to a more homogeneous temperature distribution.
We manufacture engineered products from high-quality hot work tool steel or corrosion-resistant premium metal powder from BÖHLER or Uddeholm. The ready-to-use products undergo all the necessary processing steps to meet the customer’s specific requirements: state-of-the-art mechanical machining processes, optimum heat treatment, wear-resistant PVD coatings from Eifeler, or design and functional textures from Eschmann Textures.
-
Additive manufacturing provides an excellent basis for the implementation of our engineered products, for example for plastic injection molding. The ability to implement intricate, internal details as early as the tool design stage means that features such as venting structures with microscopic porosity can be realized structurally. This enables targeted mold ventilation—and thus ensures that no air pockets remain in the mold during the injection process. This prevents defects.
In aluminum die casting and plastic injection molding, shorter cycle times can be achieved in component production by using AM to produce customized conformal cooling-channel designs (compared to conventionally manufactured tool inserts). Conformal temperature control also ensures a more homogeneous temperature distribution during the injection molding process, which reduces distortion and can therefore lead to lower rejection rates. AM also enables the production of internal channels for the integration of sensors—without affecting mold temperature control—in order to record real-time data and monitor quality characteristics.
On three continents, our additive manufacturing centers are always close to the customer for the implementation of tool ideas.
Services
Through our global network, we provide day-to-day support for our customers in the tool industry. Around 130 locations worldwide offer comprehensive help with questions and challenges relating to toolmaking.
Even before tools are used for the first time, the right basis for the best possible tool performance can be established with optimum heat treatment and a precisely matched coating, e.g., PVD.
-
Heat treatment is essential for greater material strength, better wear resistance, and improved corrosion behavior of tools. We offer a wide range of heat treatments through our global distribution network. This enables us to optimize our products for individual customer requirements.
There are currently 58 locations around the world for the heat treatment of tool steels, e.g., high-alloy cold work tool steels, hot work tool steels, plastic molding tool steels, high-speed steels, powder metallurgy steels, and special materials. Our most important services there include:
- vacuum hardening for greater material strength, better wear resistance, and improved corrosion behavior of the components;
- gas and plasma nitriding, for extremely hard surface layers and even better wear resistance
- induction hardening for steels with a carbon content of at least 0.3%: The tool surface is brought to hardening temperature using an inductor (only at selected locations).
-
A few micrometers make all the difference. The wafer-thin coatings applied to tools by the voestalpine eifeler Group make a significant contribution to greater hardness and less wear.
- PVD (Physical Vapour Deposition) coatings in a high vacuum: Metal is converted into a vaporous state and a reaction gas is added at the same time. Due to different temperatures (in excess of 200 °C), layer thicknesses of 2–8 µm are deposited on the tool.
- CVD (Chemical Vapor Deposition) coating, on the other hand, is the deposition of hard coatings. At temperatures of approx. 1,000 °C, the gaseous coating components flow around the mold and react with elements of the mold surface to form a coating. These coatings are also known as heavy-duty coatings due to their very good adhesive strength combined with very high hardness.
Coatings are applied to high-alloy tool steels, HSS and PM materials, and carbides. After coating, steel tools must be subjected to post-heat treatment in a vacuum. As the choice of material and the processing steps to be coordinated with the coating are a complex matter, particularly due to the post-heat treatment required, we remain in close contact with our customers right from the start.
-
High demands are placed on tool steels and the tools and dies made from them. Given that their production involves a great deal of effort, performance-preserving measures and repairs are of great interest. Wear protection through repair welding is very economical and especially attractive for very expensive tools and molds.
Although the weldability of tool steels is a major challenge, thanks to the expertise of the voestalpine Böhler Welding Group, we are able to offer solid and durable solutions for wear protection welding consumables. They are used in a wide variety of areas in the tool industry:
- when designing new tools;
- when rebuilding and repairing cracked or worn tools;
- when renewing the cutting edges;
- to rectify production errors and for design changes; and
- for partial reinforcement of components subject to heavy loads.
Our product portfolio consists of a wide range of stick electrodes, TIG and MIG wires, cored wires, and metal powders that have been specially developed for welding cold and hot work tool steel.