The megatrends impacting the automotive industry are challenging manufacturers and their suppliers to make strategic decisions with respect to sustainability, decarbonization, and electrification. voestalpine’s expertise across its four divisions supports leading OEMs and automotive suppliers in this unique period of transformation. Our specialisms include:
- Lightweight construction
- Body panels
- Engineered products
- E-mobility and other powertrains
- Safety systems
- Wire products
- Welding consumables
as well sustainable solutions for the automotive industry.
Lightweight construction and safety
Lighter vehicles require less drive power. We provide automotive manufacturers and suppliers with solutions that reduce a vehicle’s weight without impacting its safety.
-
These include our components made from phs-ultraform® and phs-directform®—lightweight vehicle components made from press-hardened, galvanized steel. They are used in safety-relevant locations including A and B pillars, cross-members, and sills.
-
Our “ultralight” steels help reduce vehicle weight while improving crash performance. The ultra-high strength steels for cold and hot forming are ideal for manufacturing complex modules used in the passenger compartment, autobody parts, seat rails, profiles, and many other areas.
-
Our tailor-welded blanks in various steel grades and plate thicknesses are used to produce customized component properties—vital for greater crash safety while simultaneously reducing vehicle weight.
Body panels
-
Large exterior body panels are designed to catch the eye on modern vehicles, making them one of the most sophisticated segments in our product range. We manufacture parts from steel or aluminum sheet on fully automated press lines, using tools up to 5 meters in size, for
- doors,
- side panels,
- hoods, and
- fenders.
We also make assembly parts, such as doors, trunk lids, and engine hoods. This involves complicated joining technologies such as laser welding and brazing, clinching, gluing, riveting, and roller hemming.
-
voestalpine Böhler Welding products cover the complete range of welding and brazing applications for automotive construction, guaranteeing that all automotive components are securely joined. This includes welding and brazing applications for structural parts, autobody parts, exhaust systems, and brazing applications used in e-mobility, as well as drive components for the powertrain, gearbox, air-conditioning, battery modules, and electric motors.
Engineered Products
We work together with our automotive customers to develop engineered products. These are ready-to-use parts made from high-quality steel grades or premium metal powder. We offer products made using both additive manufacturing and conventional production processes.
They undergo all the necessary processing steps such as surface treatment, heat treatment, and coating in accordance with the specific requirements.
-
Almost 60% of all cast parts worldwide are used in automotive construction, as cylinder heads in engines, in air-conditioning systems, in safety belts, etc. We provide manufacturers of extremely thin-walled die-cast components with a complete range of offers. We work with them to develop die casting molds that optimize the cooling phases. As a result, our customers profit from lower reject rates, reduced downtime, and significantly increased energy efficiency. Die-cast components are produced either using conventional manufacturing processes or additive manufacturing (3D printing), as required.
-
Injection molding is one of the most popular processes used in manufacturing plastic products. This highly sophisticated process can realize a huge variety of extremely precise shapes and structures, predominantly for use in the automotive industry.
Whether designed to mimic the appearance of wood, fabric, or leather, plastic injection molding tools create perfectly structured surfaces for use in vehicle interiors. Our engineered products for plastic injection molding are produced using either conventional manufacturing processes or additive manufacturing (3D printing), as required.
-
Our engineered products services are another piece in our long value chain. The High Performance Metals Division has its own sales and service network and offers a focused portfolio of services:
- additive manufacturing,
- coating,
- heat treatment,
- processing and cutting services, and
- warehousing.
E-mobility and other powertrains
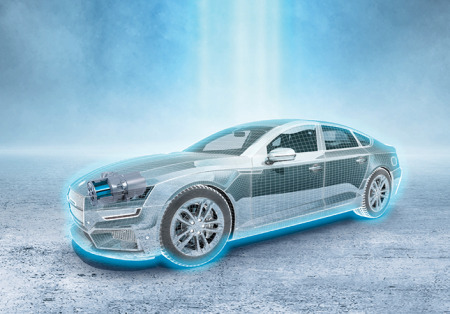
At our production facilities around the world, voestalpine manufactures components for motors, for the transmission of drive power, and to meet the specific requirements of different powertrains: including valve steel, electrical steel strip, engine mounts, and fuel tank vent pipes.
-
Whether powered by electricity, biofuels, or conventional fuels, we apply voestalpine expertise to support all drive systems. They include fuel tank vent pipes and fuel injection pipes, as well as turbocharger shafts made from cold heading wire, all of which play an important role in high efficiency combustion engines. The materials used to construct the inlet and outlet valves used in every combustion engine must be particularly robust. Our valve steels are capable of withstanding the permanent thermal and mechanical stresses as well as corrosive attack from engine exhaust emissions.
In the automotive industry, electrification of the powertrain is a key trend in current developments. We support OEMs and the supplier industry with intelligent technologies and sustainable material solutions.
-
Our high efficiency electrical steel strip isovac® and isovac® high strength are designed for compact construction in electric drives. isovac® is our non-grain oriented electrical steel strip and plays a vital role in achieving high levels of energy efficiency in e-mobility. Highly effective insulating varnish on the strip surface enhances performance. Our electrical steel strip is used in constructing stators, rotors, and servomotors.
-
Group company voestalpine BÖHLER Welding offers special brazing consumables for e-mobility applications. One example is their brazing foils, used for resistance brazing in battery systems and drive components.
-
Our broad range of lightweight construction products supports OEMs as they strive to expand electric vehicle driving ranges. They include our rotor shafts made from seamless precision steel tubes for weight-saving applications in electric drives.
Safety systems
-
Drivers should arrive at their destination safely. That’s why we are working across the Group to create products for highly effective safety systems. Our focus lies in the broad range of passive safety components incorporated into a vehicle body, such as bumpers, integral, cross and side members made from high-strength steel which absorb impact forces in crash situations.
-
Hundreds of millions of tailored tubes for belt and buckle tensioners, hood lifters, and airbags are helping protect vehicle passengers and other road users worldwide.
In addition to their use in safety systems, tubes are used in many areas of modern vehicle construction, including autobody parts and elements in steering, seating, and suspension systems.
Wire products
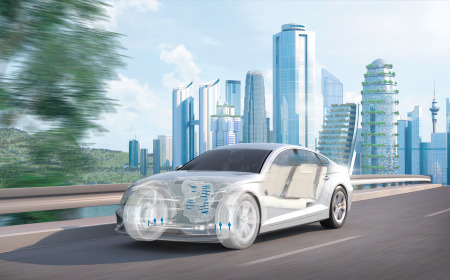
Our high-quality wire solutions serve as prematerials in many automotive applications. voestalpine Wire Technology is a leader in the production of wire rod, cold heading wire, flat and profile wire for sophisticated automotive applications.
Irrespective of the powertrain, every passenger car contains around 80 to 120 kg of our premium wire. As these products are all highly safety-relevant, wire for the automotive industry must be fine grained, with a highly uniform microstructure, and free of cracks and irregular alloy accumulations.
There are many areas of application for wire in the automotive industry, including:
- torsion bars in occupant restraint systems for safety belts,
- valves for ABS units,
- components for gas generators in airbag systems,
- ball studs in passenger car steering systems,
- axle, vibration damping and clutch springs in the chassis,
- roller and ball bearings in engines, chassis, gearbox, as well as
- high and ultra-high strength connecting elements for dynamic load stresses.
Welding consumables
Welding is the most commonly used joining technique in automotive construction. Welding and brazing consumables from voestalpine BÖHLER Welding are used in passenger vehicles worldwide. Whether in the autobody, powertrain, or exhaust system, conventional combustion engine or e-motor, we offer the ideal consumable for every application. Also for accurately welded visible seams on aluminum body panels, executed using our own special in-house welding process.
Around the world, the highly effective, sustainable solutions offered by our voestalpine companies play a role in the success of the automotive industry and its suppliers. You will find more detailed information about our automotive products in our product search.