As one of the world’s leading suppliers, our range of products for the aerospace industry includes:
- High-performance materials such as special steels, nickel-based and titanium alloys
- Finished components for engines, fuselages and landing gear as well as
- Products and services for the aerospace industry.
Our companies work in close collaboration on aerospace projects to make sure our customers benefit from our shared voestalpine expertise. To mark this collaboration, we have launched a joint market presence for our companies on the voestalpine Aerospace platform.
High-performance materials for aerospace
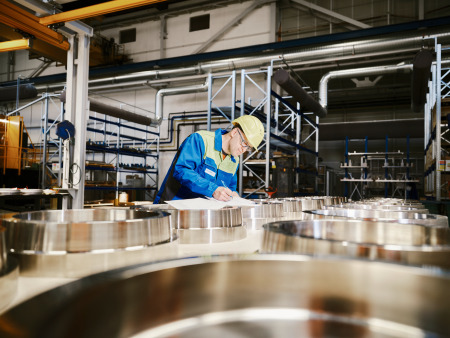
Our materials for the aerospace industry have made voestalpine an industry leader in the aerospace sector and help make air traffic safer and more sustainable. We produce the optimal alloys and apply the latest knowledge on manufacturing and processing techniques. We develop suitable materials and treatment methods recognized and approved by the leading testing organizations for every application. Our high-performance materials are either delivered directly from our production sites or via our global service centers in the form of rods, billets, sheets, plates, and custom parts.
-
Nickel-based alloys are characterized by a high degree of toughness as well as strong resistance to oxidation and corrosion. By adding special alloying additions to the base nickel content, we can create materials that offer impressive properties for particularly critical applications.
As the reason behind the name, nickel forms the main component of nickel-based alloys. We employ alloying elements such as chromium, molybdenum, cobalt, tungsten, and aluminum to make our nickel-based alloys resistant to high operating temperatures and extreme conditions. Depending on the required properties, our nickel-based alloys typically contain at least ten different alloying elements.
Nickel alloys are primarily open-cast melted with vacuum induction melting depending on the requirements and alloy application. Following melting, the alloys are then generally remelted according to the electro-slag remelting process or the vacuum arc remelting process to improve the homogeneity and purity grade. The main advantages offered by nickel-based superalloys are their
- creep and fatigue resistance at high temperatures, exceeding the performance of highly heat-resistant steel grades at temperatures in excess of roughly 550°C;
- ability to be used at temperatures up to 750°C;
- resistance to corrosion thanks to the formation of very thick oxide layers.
We recommend our nickel-based alloys as the best choice when designing airplane turbines on the basis of these special properties. They are even employed for space projects in the aerospace industry.
-
We equip our special steels for the aerospace industry with the parameters our customers are looking for. From the way in which they can be processed, e.g. during machining, to a special, defined expansion coefficient as well as magnetic or anti-magnetic properties. Decades of experience in developing and manufacturing selected steel grades ensures we uphold the high quality requirements in the aerospace industry.
We put our extensive knowledge and state-of-the-art facilities for melting and remelting technology to use in order to manufacture our products: vacuum induction melting units (VIM), vacuum arc remelting units (VAR), and pressurized electro-slag remelting units (PESR).
Our special steel grades are used in the production of
- side panels in airplanes;
- cargo systems/entrance doors;
- pylon and fuselage mounting brackets as well as
- components for turbines and landing gear.
-
Titanium is a fixed component in our aerospace portfolio, particularly with the increased focus on titanium as a material in the aerospace industry. Titanium possesses a number of properties that make it particularly suitable for lightweight construction in aerospace:
- 40% lighter than steel;
- high strength;
- extremely high thermal and mechanical resistance;
- high resistance to corrosion—even when not coated; and
- particularly suitable for use in engine and structural components.
Titanium offers one special advantage when it comes to modern hybrid construction: When heated up, components made from titanium only change their dimensions half the extent as steel, and only one third of the extent of aluminum. Accordingly, titanium’s coefficient of thermal expansion is roughly the same as for carbon fiber, making it particularly suitable for processing with this metal.
Titanium and titanium alloys are ideally suited to a wide range of applications. Needless to say, we comply with the strict specifications made by our customers in the aerospace industry. We produce and sell titanium products in alloyed and unalloyed form as forged parts, sheets, plates, and bar stock.
-
Our high-performance materials are also available as high-quality powders made from steel as well as titanium-, cobalt-, and nickel-based alloys. These powders provide the ideal basis for additively manufacturing components. We optimize the properties of materials to ensure top performance.
Our product portfolio is constantly being expanded to include the latest innovative developments. We can draw on our proprietary portfolio of roughly 250 alloys to meet customer-specific requirements. Our production plants and metallurgy expertise allow us to customize alloys. Vacuum induction melting and atomization with the use of inert gas guarantee top product quality.
Components for the aerospace industry
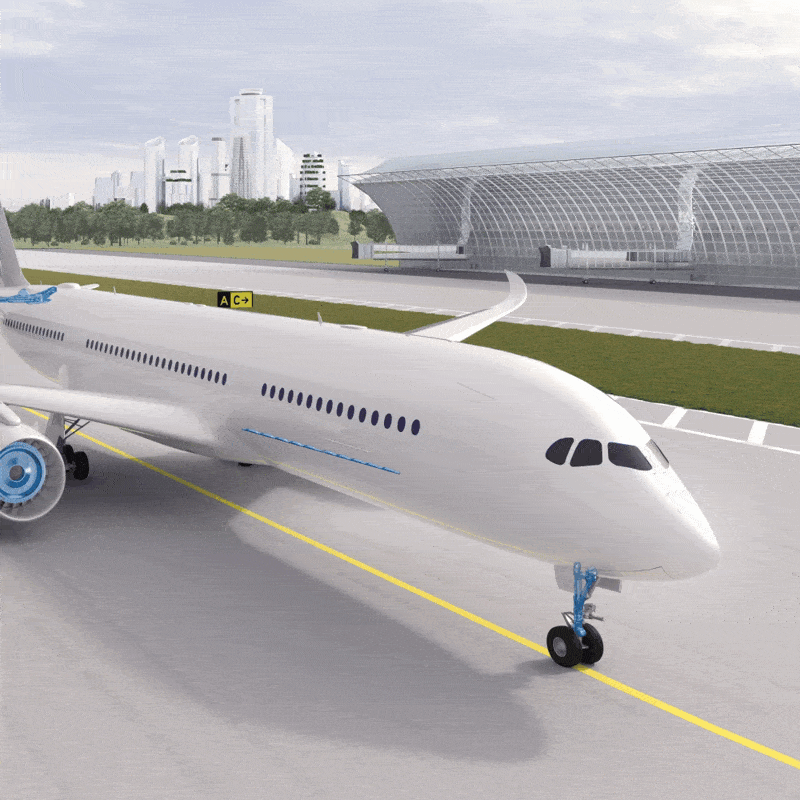
As a manufacturer, we know our materials best. With this in mind, we apply our expertise when it comes to transforming our materials into components that are directly sent to renowned aircraft manufacturers and their direct suppliers. Whether they will be put to use as a structural part, in engine components, or in the landing gear, our efficiently manufactured high-precision components can be found in virtually every plane on the planet.
-
Modern airplane propulsion systems involve impressive speeds and operating temperatures. Capable of up to 20,000 rpm and working at temperatures up to 1,600°C, engines and turbines are exposed to extreme conditions. We use high-performance materials to produce components designed to withstand highly fluctuating temperatures and constantly changing conditions to ensure high operational performance. The quality requirements to which the materials are subject require constant certifications and individual customer approvals. We routinely meet these standards and develop further innovative solutions in partnership with our customers.
- Special profiles for engine components:
e.g. for static turbine rings and engine guide vanes; - low-pressure turbine disks for regional jets and single-aisle airplanes to large low-pressure turbine disks for long-haul aircraft and twin-aisle airplanes;
- engine components for helicopters and planes, e.g. engine disks;
- parts for pylons (engine boom).
- Special profiles for engine components:
-
Sealing profiles from RFC In aerospace, a combination of flexibility and strength at high pressure are decisive when it comes to lasting performance. When the wing tips are raised and lowered by up to two meters during take-off for a plane like the A380, the transition points between the wing and fuselage are exposed to enormous forces. To counteract this, leading manufacturers equip wingboxes with components manufactured by us with the power of the world’s largest screw press.
We supply the following components, among others, for the safe construction of airplanes:
- wing components;
- engine mounts capable of withstanding thrust in excess of 200,000 ps;
- main support elements for wingboxes, the load-bearing joint between the fuselage and wings;
- stringers and other structural parts for airplane fuselage;
- sealing profiles for loading hatches;
- special profiles for seat tracks, including made from titanium;
- special profiles for engine components;
- parts for tailplanes.
-
In order to safely touch down on the ground, landing gears are often required to safely carry several hundred tons of landing weight and absorb hard impacts. The retractable, generally steerable structures therefore need to provide high performance at all times. Their resilience is put to the test during the endurance test on a test bench, whereby the components need to prove their ability to withstand temperatures between -60 and +85°C as well as under millimeters of ice; all while withstanding one and a half times their maximum operating load.
Made from special steels or titanium materials, our landing gear components reliably withstand these loads.
-
Components used in space travel undergo particularly rigorous and tough trial and test stages. Our components for the ESA rocket Ariane 6 passed all tests with flying colors, just like with its predecessor. We supply complete components for use in the launcher, including the starter housing for the Vinci rocket engine.
This component is fully sourced from our production chain: from melting the nickel-based alloy to remelting, forging, heat treatment, and testing, ending in finishing.
Technological excellence for aerospace
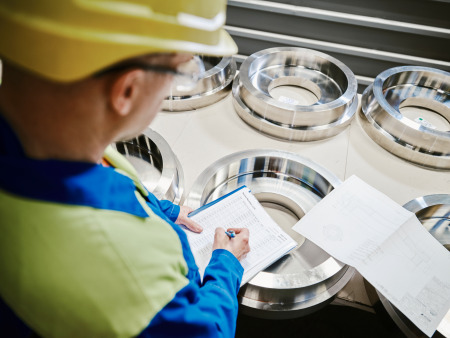
We meet the high requirements of the aerospace industry with technological excellence. We are guided by all the requirements communicated by our customers, including growing demands for sustainability and efficiency. Our production companies possess all necessary certifications and special customer approvals from all leading manufacturers in the industry.
-
Achieving a cost-effective buy-to-fly ratio means using as little valuable input material as possible in components—a target that also drives the aerospace industry. Our near-net-shape forging is the perfect solution:
- It is designed to simplify and minimize the amount of machining work required when the component is finished at the customer’s premises.
- Near-net-shape forging makes it possible to use input materials in a more sustainable manner to conserve resources.
We use tools such as the world’s largest screw press for near-net-shape forging. With a press force in excess of 35,000 tons, at voestalpine BÖHLER Aerospace, we can manufacture products in strict compliance with customer-specific quality requirements. This also applies to the manufacture of side load fittings on the joint between the airplane fuselage and wings, for example.
We also provide a simulation of the forging process and heat treatment in order to estimate the material properties and potential component stresses for optimum efficiency when finishing the part.
-
Thanks to our titanium products, we are Europe’s only manufacturer for semi-finished and finished components for use in the aerospace industry. We have employed our expertise in processing high-performance materials to manufacture titanium products. Two of the special advantages offered by voestalpine Böhler Bleche include rolling and flattening titanium plates. To achieve this, we have adapted our process sequences on the two-high rolling stand as well as the heat treatment cycles to this material. We utilize a special vacuum flattening system to flatten titanium plates with particular evenness and low stress—all in line with our customers’ requirements.
In order to produce complex titanium structures, our aerospace experts from the voestalpine Roll Forming Corporation, for example, use the most effective and safest processes, two of which include high-precision roll forming and welding methods designed to make airplanes safer and more efficient.
-
When it comes to supplying airplane manufacturers, our strengths also lie in our roll-forming expertise. We deliver effectively formed high-performance components to suppliers and OEMs in the aerospace industry from our locations in Asia, Europe, and North America. The manufacturing portfolio of voestalpine Roll Forming Corporation also includes deformation with variable thicknesses, heat treatment, precision drilling, five-axis precision machining, thermal processing, titanium and laser welding, and many more products and services.
Custom profiles made of high-performance materials such as titanium perform an indispensable and safe job when used as seat tracks to anchor passenger seats to the floor in commercial aircraft.
-
Based on the competence of voestalpine Böhler Welding, we are also able to offer suitable systems and welding consumables for safely welding aerospace components. In order to meet the high requirements in the industry, we provide welding equipment, consumables, and other products for tungsten inert gas welding (TIG), a process that permits particularly high-quality welding for aerospace applications thanks to the use of inert gas.
We offer a wide range of tungsten electrodes to support this welding method. The success of TIG welding can therefore be significantly improved by using coordinated welding machines with intelligent functions, such as the Böhler Welding EasyArc.
-
Our expertise in additive manufacturing is also employed in the production of airplane components. Components can be built in the 3D powder bed printing process Wire Arc Additive Manufacturing to reduce their weight and cost. To achieve this, titanium wire is welded on in layers to gradually form the component.
3D printing can be used for building lightweight structures to reduce the all-up weight and make air travel more sustainable in the process. On three continents, our additive manufacturing centers are always close to the customer for the implementation of ideas.
-
Coatings protect the surfaces of components and help to limit wear—key prerequisites for the sustainable use of airplane components. Our eifeler coating center in Schnaittach, Germany, is one of the few companies that offer PVD coatings for the aerospace industry in line with the requirements set by NADCAP and Rolls-Royce. Our coating facilities are specifically certified for aerospace. Exclusive material flows for aviation materials help to ensure high quality standards are met.
We offer titanium-nitride (TiN) coatings for flight bearing rings in the aerospace industry, for example. Layers of TiN between 2 and 6 µm thick offer excellent protection against wear, abrasion resistance, and help prevent cold welding.